Silence Is Golden: PC-based Control Optimizes Noise Testing for Steering Systems
- Casey Taylor
- Jul 25, 2023
- 6 min read
Precision measurement I/O terminals boost final inspection and quality assurance in automotive applications
Nobody wants to hear cracking, scratching, knocking or whirring while driving. But how can subjective noise perception of a human be quantified and measured objectively for correction? As a leader in this area, thyssenkrupp Presta measures structure-borne noise during end-of-line automotive testing.
Just a few moments are crucial in the life of a vehicle’s steering system – one key moment is when thyssenkrupp Presta puts it through its paces in an end-of-line test rig, as it does with every steering system. In addition to various functional tests, the noise generated plays an essential role. “Acoustic testing is about ensuring that drivers do not perceive any annoying noises while driving,” explains Joachim Sutterlüty, head of automation at thyssenkrupp Presta.
Translating these noise perceptions into measurable values is the job of the experts at the thyssenkrupp Presta acoustic center of excellence. Together with manufacturers, they analyze and define noise behavior right from the development stage on prototypes and pilot series, and they measure subjective acoustic properties in objective terms. This noise profile and its permissible limits later form the basis for measuring structure-borne noise in production.

If the noise spectrum of a steering system lies outside this profile, it is returned from the test rig to a rework station. Then the measured structure-borne sound spectrum is used to decide whether to rework or disassemble the component, explains Sutterlüty: “With our sensors, together with the measurement terminals and PC-based control from Beckhoff, we can evaluate the noise so precisely that the worker can narrow down the cause of the noise accurately based on the displayed spectrum.”
Structure-borne sound is complex
Steering system prototypes undergo a whole battery of test before a noise profile of this type can be developed. Accordingly, thyssenkrupp Presta has numerous test rigs in operation in the prototype shop, where the acoustics of a steering system are designed. These must then be adhered to in the fully automated assembly plant.
“Our development is incredibly dynamic with frequently changing variants, so we need a very high level of flexibility,” Sutterlüty says.
To deliver this flexibility, Presta designs and automates all test rigs completely in-house, purchasing only the mechanical setup and electrical components. For the latter, the automotive supplier has relied on Beckhoff components for more than 20 years. And it has recently adopted powerful new tools for high-end measurement technology, the ELM3604 EtherCAT Terminals and TwinCAT Scope software for measurement data acquisition. This approach saves significant engineering work and time, in addition to a great deal of space and cost.
High-end measurement terminals replace stand-alone system
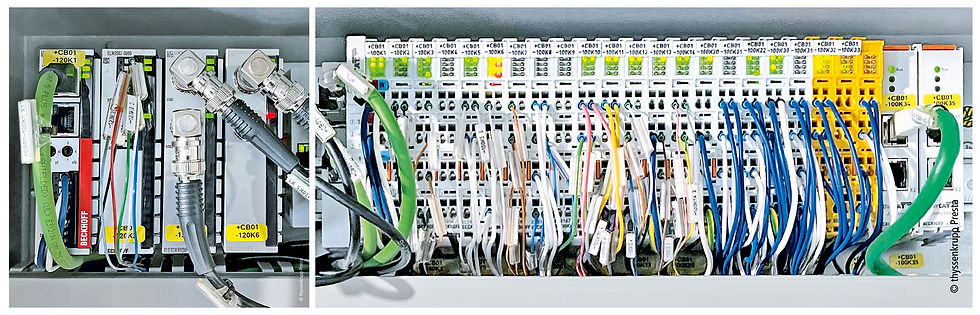
The previous concept was based on an external system for acoustic testing. This required complex interfaces and signal splitters for the actual test rig control system, according to Michael Sauerwein, electrical engineer at thyssenkrupp Presta. “This equipment alone required a separate control cabinet and repeatedly caused problems during commissioning, from complex EMC shielding to double calibration and wiring errors,” he says.
On top of this, project planning, configuration and programming of the separate system created additional complexity. With PC-based control, EtherCAT and the high-end measurement terminals from Beckhoff, the test engineering experts eliminated these interfaces, gaining significant flexibility and time with massive reductions in complexity and costs. “Roughly speaking, we save about 5% of the investment costs per test module,” says Sutterlüty.
In 2020, the new concept was intensively tested and examined in an initial testing plant in Eschen, Liechtenstein. The Beckhoff technology was then integrated into the test field and the sensor signals were tapped in parallel with a previous system to verify the results. After all, some sensor signals must be recorded synchronously at a high resolution with 24 bits and up to 20 ksamples/s.
So, would the high-end measurement technology from Beckhoff come close to the external system? That question was on the mind of Acoustics Expert Julius Ellmann. “We wanted to see if we could replace the old system with something that would live up to the same measurement quality,” Ellmann says.

The short answer was yes. The Beckhoff-based system met all requirements for metrological complexity, and at a much better price point than the legacy test system. This is because the ELM360x EtherCAT measurement terminals are directly integrated into EtherCAT. They are also very flexible in terms of the number of channels and – with TwinCAT Scope – are very quickly configured for data collection.
“As part of the changeover to ELM measurement technology, we were able to increase the number of measurement channels due to the advantageous price,” Ellmann adds. “Together with optimized sensor technology, we were also able to enhance the measurement quality.”
Resolving the software interface bottleneck

The success of the changeover was due in no small part to the flexibility and openness of PC-based control. This was confirmed when TwinCAT was integrated into the external evaluation software. As it turned out, the engineering team couldn’t just get rid of the existing measurement software from the previous vendor because other departments use functions of the software. “But the TwinCAT Scope API from Beckhoff is a powerful interface for reading out the data,” says Maurus Kaelin who works in sales at Beckhoff Switzerland.
However, the interface of the evaluation software turned out to be a bottleneck. “We had to optimize the software interface so that the data packets could be received and analyzed quickly enough,” recalls Karsten Mauersberger, who develops test rig software at thyssenkrupp Presta.
Pascal Dresselhaus, Product Manager TwinCAT, was on hand with his Scope development team to work with thyssenkrupp Presta and the test and measurement software provider. This empowered the engineers to achieve the best possible performance for the application. “Joachim Sutterlüty and his team set out their requirement for a powerful, state-of-the-art interface for data acquisition,” recalls Dresselhaus.
Many TwinCAT users are familiar with TwinCAT Scope only from its integration in Microsoft Visual Studio for measurement data analysis and machine commissioning. However, in addition to the front end in the TwinCAT engineering environment, there is also an extensive application programming interface (API) for TwinCAT Scope (TE1300). Especially in the .NET environment, this can be used to integrate the charts of a Scope View as a Control in your own visualization, for example. This finalizes all of the charting, including the back end with the Scope Server. Many Scope properties are highly customizable, so in some cases it may not even be possible to identify TwinCAT Scope from Beckhoff as it runs in an application.
In this specific case, however, the API was not used in the conventional manner for the visual display, but instead for relaying the recorded measurement data from the ELM3604 terminals. Using sample code with sophisticated data buffers, smooth integration with the third-party software could be ensured. “In terms of functionality, it was possible to implement the application based on the current state of the Scope API. Our support essentially consisted of writing a best practice for using high-resolution data,” Dresselhaus says.
The openness of the software solution was an important criterion for thyssenkrupp Presta. This was highly advantageous when it came to integrating the evaluation software and the many export formats. At the same time, thyssenkrupp Presta also retains the ability to use the analysis options in TwinCAT.

“All options are available, particularly those involving TwinCAT Analytics,” Dresselhaus adds. “We have great engineering products for data analysis with over 100 algorithms. From the cycle times of the test rigs to frequency analyses of noise development, as soon as the data is available in the Scope format svdx, TwinCAT Analytics can be used to find many needles in the data haystack.”
Global roll-out under way
What began around two years ago with an initial concept is now proving itself in practice. In addition to the test rig at the company headquarters in Eschen, the first systems are already in regular operation at the production plant in Hungary. “Further systems are currently on their way to China and Mexico or are already being set up there,” Sutterlüty says.
Due to the results in the areas of both measurement accuracy and test speed, as well as the much simpler implementation and commissioning processes, the concept based on EtherCAT Terminals with high-end measurement technology will form the basis for all further acoustic measurement modules. In the future, all new acoustic test systems in the production area will be equipped with it. That is because the advantages of PC-based control are compelling, as Sutterlüty explains: “We can completely replace external measurement hardware.”
Ready to take your test and measurement tech to the next level? Reach out to your local Beckhoff sales engineer today.

Casey Taylor is a Software Product Manager at Beckhoff Automation LLC
Comentários