How to Reach the Finish Line in Cabinet-free Machine Design
- Eric Reiner
- Feb 2, 2024
- 7 min read
Updated: Mar 25
The benefits of cabinet-free machines are attainable for both OEMs and end users with reasonable goals and a phased approach

If you want to run a marathon, you don’t just show up the morning of with worn-out sneakers and good intentions. Runners follow training regimens. They tackle progressively longer races – a 5K, 10 mile, half marathon. This way they’re set up to succeed when the big event arrives.
Designing your way to a cabinet-free machine is similar. New machine control technologies are helping leading-edge systems begin to ditch the enclosures previously needed to protect power supplies, I/O, networking, HMI, control and other equipment from harsh production environments. If you want to reap the many benefits of eliminating electrical cabinets, there are many smaller steps you can take first.
When you start down this path, there are many advantages for machine builder OEMs and equipment end users alike. A complete machine-mounted control system can dramatically reduce overall costs. Beyond getting rid of the enclosure itself, your machine no longer needs fans, filtration systems, cooling equipment and the associated power to run it all. With standard connectors on all components, you reduce wiring time, eliminate wiring errors, and cut documentation dramatically.
Manufacturers can reduce footprint requirements to pack more machinery into the same square footage. And emerging modular options for cabinet-free machine control help simplify everything from wiring and installation to support and spare parts inventories.
But let’s not get ahead of ourselves. To see how to get from a cabinet-dependent design to a cabinet-free one, it’s important to understand the various steps it’ll take to get there.
Level 1: Distributed I/O for data acquisition and more
So what’s the 5K run in this scenario? That would be: adding functionality without expanding the control cabinet.
The place to start is adding remote I/O and IP65/67-rated machine controllers, like the C7015 ultra-compact Industrial PC, that don’t require the protection of an enclosure. While ruggedized I/O blocks in IP67 or even IP69K are not exactly new, the strategic application of these technologies has offered significant advances in many applications. These devices gather more data in more places, whether that’s for communication, acquiring signals from sensors, integrated functional safety and more. By distributing the I/O closer to the end devices, you’ll seriously cut back your cabling runs as well.
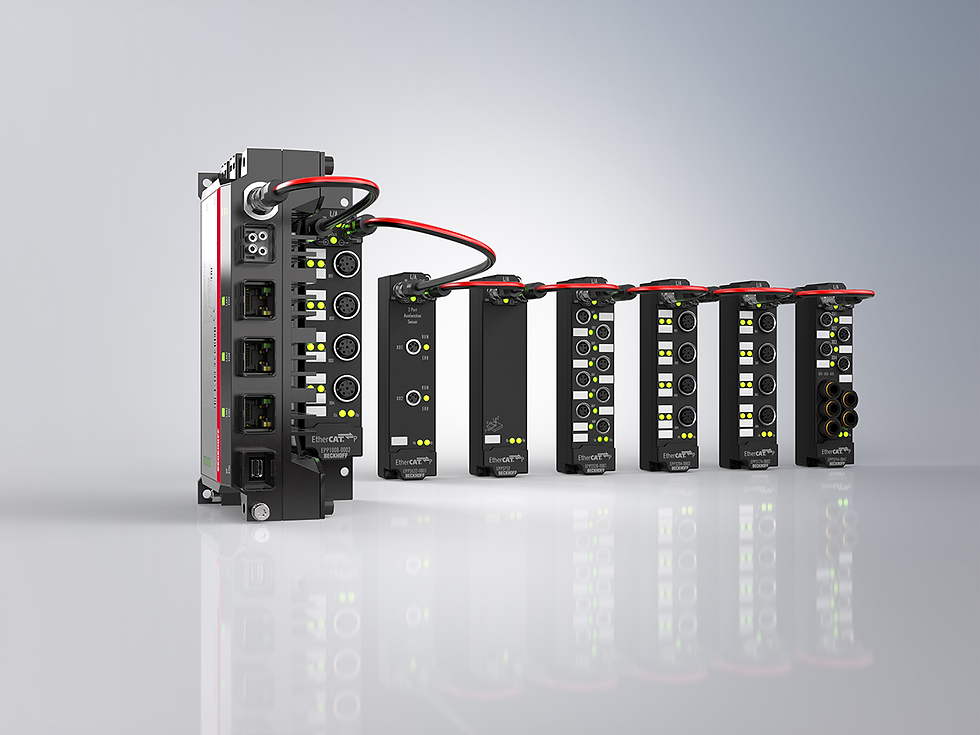
Industrial PC (IPC) solutions that can be installed in the field, however, offer completely new possibilities. Leveraging these technologies doesn’t necessarily mean you’re using the control hardware to run the machine. The IPC could handle control logic for a specific machine module that can be unplugged and moved around the factory floor.
In brownfield applications, one of these IPCs could be added as an IoT gateway or edge computing device. Flexible mounting options make it easy to physically attach the controller where it makes the most sense. This eliminates the need to find space in the cabinet and worrying about the additional heat source, along with the need to run multiple cables all the way back to the cabinet. With a port for EtherCAT P, which combines power and communication in a standard 4-wire cable, the controller can easily support the addition of I/O blocks for data acquisition or special functions.
Equipped with an analytics software package, the IPC could perform some preprocessing of data, then send important metrics to the enterprise or cloud level using a cellular or Wi-Fi transmitter. This is a great option if you have older equipment that still meets throughput and quality requirements but needs to provide data to measure machine health or energy efficiency. And, of course, that’s just step one.
Level 2: Machine-mountable control and distributed motion control
The next level is actually shrinking control cabinet requirements for new machines. Technologies to build completely cabinet-free machines are continuing to evolve, and many engineers are taking a wait and see approach. However, numerous machine-mountable devices are already available to minimize the need for large, protective enclosures.

Employing a dual- or quad-core cabinetless C7015 IPC as the main machine controller and using servomotors with integrated drives, such as the AMP8000 series from Beckhoff, makes this possible. Some electronics – power supplies, fuses, contactors, etc. – may need to remain in an enclosure, but with these cabinet-free options, the necessary footprint shrinks dramatically.
We’ve seen numerous systems take this route. Typically, they use an IP65/67 IPC or a fully enclosed panel PC, which combine the machine control CPU with rugged HMI hardware. Building on the remote I/O solutions and EtherCAT P communication, a distributed servo drive system allows the machine builder to incorporate dynamic motion control without needing to reserve a large section of the electrical cabinet for separate drives.
These distributed servo drive solutions integrate the amplifier directly onto the back of the motor. An IP67 distribution module streamlines daisy-chaining for systems with advanced motion requirements. The distribution module can also connect via EtherCAT P to other sensors, actuators and more, enabling a complete machine with greatly reduced requirements for electrical enclosures.

In addition to stationary machines in packaging, intralogistics, assembly and other industries, these types of solutions are ideal for mobile robotics. Automated guided vehicles (AGVs) and autonomous mobile robots (AMRs) both have extremely compact enclosures. The option to include a controller on the exterior or at least in a space that’s partially exposed to harsh production environments offers a significant level of flexibility.
In either case, the PC-based controller could also consolidate several functions that usually require separate hardware, for example, PLC, safety, machine vision and navigation. This level of cabinet-free control could be your stopping point – or it could launch you into the next challenge. Just like a runner working up to that big race, the cabinet-free machine controller, I/O and servo solutions should build upon proven technologies.
Level 3: Complete cabinet-free control
The final level is ditching the cabinet entirely. The technologies required to make this happen remain a work in progress, since not every type of device needed for control and automation is available in IP65 or higher. That is, not yet.

New technologies, like the MX-System from Beckhoff, are entering the market that allow for a modular design of cabinet-free control. With scalable baseplates, these systems have IPCs, drives, I/O, functional safety and more as pluggable building blocks. They can be attached and secured with set screws quickly, without requiring hours of a cabinet building specialist’s time. In fact, estimates show that control system installation processes that would regularly require 24 hours or more could now be completed in just one hour using pluggable automation components in a machine-mounted platform.
Space savings also grow with this completely cabinet-free approach. Distributing the control components across the machine, rather than concentrating them in a single enclosure with numerous wires snaking back, can lead to significant footprint reductions.
We estimate that using a modular system built on scalable baseplates will offer a range of benefits, which include:
Reducing overall machine footprint by up to 70%.
Slashing the number of control components required by a factor of 10.
Consolidating documentation by as much as 80%.
Eliminating costly wiring errors through pluggable devices.
Removing numerous points of failure.
Accelerating time to market through rapid commissioning.
The fully machine-mounted control platform’s footprint and complexity reductions facilitate better collaboration between departments. For example, engineers will no longer have to design special installation spaces and brackets for the system. More modular, pluggable designs will also reduce the need to disassemble completed machines before transporting them to end user facilities.
For equipment end users, the advantages will include improved operating reliability, reduced routine maintenance requirements and simplified troubleshooting and repair, if needed. For example, some of these new solutions will feature diagnostics viewable on smartphones via Bluetooth, unique serial numbers in the form of DataMatrix codes on each module and the usual status LEDs. Using a smartphone app, technicians can scan these codes to retrieve diagnostic data from the controller and corresponding function module.
EtherCAT communication is key to providing comprehensive, system-wide diagnostics. The industrial Ethernet system also supports hot swap capabilities, which makes replacing modules, if needed, as straightforward and quick as possible.
Get in the running for cabinet-free machine design
With all of these advantages, it’s no surprise that we see engineers engaged at all levels. In fact, we’re working with machine builders to develop completely cabinet-free machines today. But it does require some reconsideration of how electrical and mechanical systems work together. Some find that level two with machine-mountable control offers all the advantages they currently need, and their end user customers aren’t asking for a more intensive redesign at this time.
Whatever level is right for you to start at, it’s important to consider the options carefully. A flexible, scalable automation platform will allow you to leverage existing software platform and design, whether you’re simply adding an IP65/67 IPC or switching to an entirely cabinet-free machine control solution.
You’ll want to make sure the leading-edge systems support open communication protocols. After all, it’s highly likely they’ll need to communicate to legacy equipment or incorporate small, remote enclosures for components that aren’t yet available in cabinet-free design.
In these cases, you’ll find that some vendors have also approached cabinet-free design as a marathon, not a sprint. Machine-mountable technologies have continued to build upon each other to get closer to the finish line. Now, machine builders and system integrators can begin deploying more extensive cabinet-free solutions – e.g. standalone IPCs, I/O and drive technology – to claim a head start when fully cabinet-free automation systems soon emerge as the main event.
Are you ready to open up new possibilities in machine design by ditching the control cabinet? Contact your local Beckhoff sales engineer today.

Eric Reiner is the IPC and MX-System Product Manager for Beckhoff Automation LLC.
A version of this article appears in Control Engineering.
Comments