Itron uses PC- and EtherCAT-based automation to help save on control hardware costs and engineering time with every assembly cell
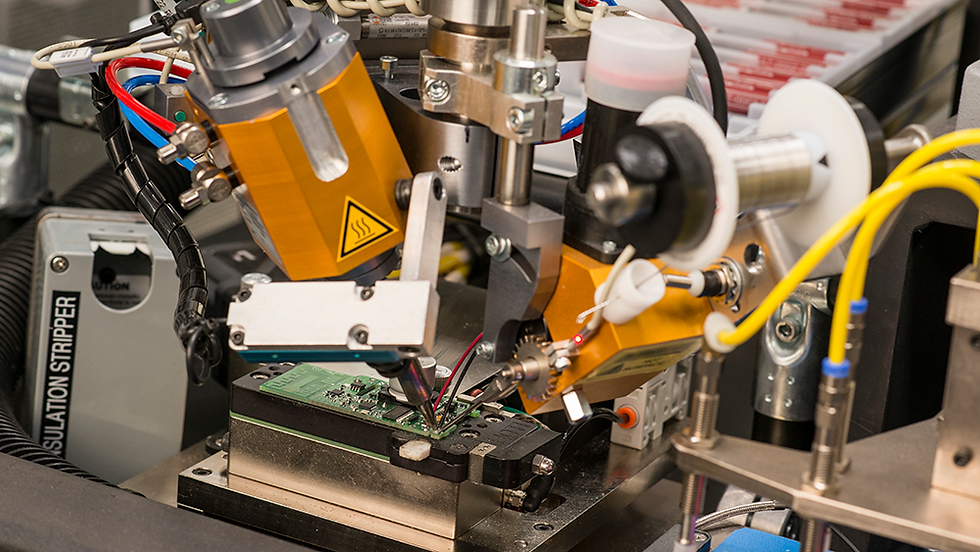
Itron is a world-leading technology and services company dedicated to the resourceful use of energy and water. The company’s Waseca, Minnesota, manufacturing facility designs and produces gas and water metering devices, also known as encoder receiver transmitter (ERT®) modules, and has engineering teams in-house that focus on product R&D, assembly and production. Currently, the Waseca facility manufactures Itron’s 100G series gas ERTs and 100W series water ERTs.
During the final few months of 2015, the facility had to significantly increase the capacity of water ERT module production. In addition, the production of gas ERTs has steadily increased each year. With rapidly increasing demands for higher production, the Itron facility is in a constant state of change. Assembly cells and lines are constantly added and retrofitted to ensure that the factory can keep up with ERT market demand.

Previously, Itron assembly cells were weighed down by a control platform that required five separate pieces of hardware for the automation and HMI systems. “This was an ongoing problem for years,” explained Moyer. “We conducted extensive research to find a successor solution to the traditional PLC for control and separate PC for HMI. Even though production levels are under constant change, a change in the control system platform can be a challenging endeavor with elements of uncertainty and risk for engineers. However, simply adding new machines of the same design was not a permanent solution.”
Complete production history, from the factory to the field
To maintain world-class product quality, Itron emphasizes comprehensive traceability from the very beginnings of assembly processes, to the supply chain, to the very end of the line when a device is purchased and installed. This ensures the best measures to quickly answer any quality question from the field, because Itron can easily pinpoint the full history of every component in every individual ERT manufactured by the company. The unique serial number of every Itron ERT is saved to a Microsoft SQL server and every production step and quality test for each ERT is recorded in the database.

For every component that goes into Itron products, a wide range of parameters are logged such as the lot code, “manufactured on” date, the component manufacturer, the date each component was used, as well as all settings and configurations on the machine that manufactured each ERT. Another large source of production data, Itron performs a series of detailed tests on all products, which can range from visual inspection, RF testing, programming tests on ERT microprocessors and more. This has helped establish total quality assurance with a complete history of every product down to the smallest component and section of code.
“This is precisely the reason we ultimately went with PC- and EtherCAT-based control technology for automation and quality assurance,” Moyer said. “It helped us establish connectivity between the automation system and remote databases while managing the incredible volumes of data to implement complete traceability.”
This line of thinking began when Itron first encountered PC-based control technology in January 2014. At this time, a European-built dispensing machine purchased for potting ERT devices arrived at the Waseca facility. The advanced machinery was equipped with a control system from Beckhoff Automation. “This was an eye-opener for us because all our previous experience was with the stand-alone PLCs and white box PCs that served as our link to the SQL database,” Moyer recalled. With Beckhoff PC-based control, Itron could streamline its system architecture with one multi-tasking controller that integrated both the PLC and PC functionality onto one powerful device. “We ended up manufacturing our own assembly systems designed in-house at Itron repeatedly over the last two years, and it has worked very well,” he added.
Major manufacturing steps at the Itron facility include soldering processes, assembly processes, potting processes to seal the ERT products (including curing after potting material is dispensed) and final testing before moving products into the supply chain. After the final automated test, there is visual verification handled by Itron production experts. Each of these steps, which are either fully automated or semi-automated, is controlled via the Beckhoff PC-based control system and EtherCAT. Some of the soldering and assembly steps utilize 4-axis articulated Stäubli robots networked via EtherCAT – these are also automated by Embedded PCs and TwinCAT software.
Shape-shifting PC-based control suits any form factor
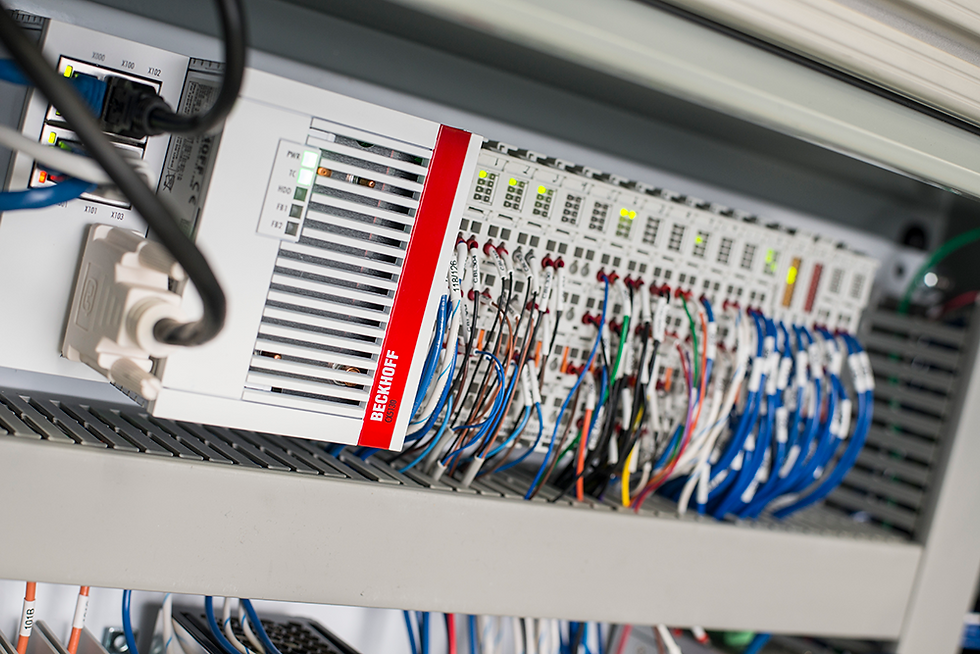
After evaluating a series of PC-based controller formats (including cabinet and pole/arm mounted versions), Itron selected the DIN rail mounted CX5130 Embedded PCs from Beckhoff. This mid-range controller features a 2-core Intel® Atom™ processor (1.75 GHz) so it can capably handle many machine functions such as PLC, motion control and HMI all on one device. At Itron, one CX5130 Embedded PC runs TwinCAT PLC software from Beckhoff for all control tasks in addition to LabVIEW software for HMI used on the same assembly cell. “Simply having the HMI software run on the main automation controller is primarily responsible for Itron decreasing cabinet space requirements and streamlining assembly cell integration,” Moyer said.
These benefits extended beyond the initial cost savings on the hardware; Itron generated even more savings because the company no longer has to write and manage revisions for code in two separate systems or create complex mechanisms just so hardware from different manufacturers can communicate. For every system the Itron team in Waseca has built since January 2014, it has reduced a previous standard of five pieces of hardware (PLC, two PCs and two HMIs) down to two – one Embedded PC and one HMI display. The savings are exponential every single time the company adds another PC-based system.

Itron has some assembly cells interfacing with the SQL database in order to send data to view production status from the floor. The Beckhoff PC-based controllers send a variety of data and parameters to the database, then production managers and operations managers from all over the world can look at the status of any line through their mobile device or laptop. The connectivity from the Beckhoff controller to the database is central to capitalizing on the data. Itron looks at everything from complete track-and-trace of manufactured product down to the component and exact time of each manufacturing step, to yield data to real‑time data for product quality.
In addition to high performance and compact controller footprint, Itron selected the CX5130 Embedded PC because it uses the Windows 7 operating system on-board and the video output to easily connect to its touchscreens. Another important factor was that the CX5130 installs easily on DIN rail in Itron’s electrical panels and directly connects to the EtherCAT I/O terminal system. The two network ports on the CX5130 are also utilized by Itron ̶ one connects to a network for the plant’s machinery, and the other interfaces with the Itron corporate intranet as the interface with internal and external databases.
Also on the networking front, Itron has switched all plant communication protocols at the Waseca facility over to the EtherCAT industrial Ethernet system. As a result, EtherCAT is used as the network for vision systems, solenoid banks and even highly articulated robots. EtherCAT has become the complete system bus at Itron’s Waseca location, increasing the speed of data transmission, pulse rates and overall cycle times. It delivers high flexibility in terms of wiring topologies and there are widely available EtherCAT devices for all industrial needs from multiple vendors. Saving considerable start-up time, TwinCAT automation software from Beckhoff automatically identifies EtherCAT devices connected to the system, regardless of vendor.

In addition to handling assembly cell control and database connectivity, Itron also uses TwinCAT for safety programming and runtime. Another key development for Itron assembly processes is programmable safety integrated into the standard automation system using TwinSAFE technology from Beckhoff. In the past, Itron implemented stand-alone safety controllers in its machine designs. TwinSAFE is highly beneficial because it is integrated into the standard controller and is managed with the same automation software, TwinCAT.
“After switching to TwinSAFE, we no longer had to handshake between the controller and the safety system; this saved a considerable amount of cabinet space while further reducing costs and programming efforts,” said Moyer. Specifically, Itron uses TwinSAFE programmable safety technology to integrate light curtains and safety for robotics and other motion functions, pneumatics and more.
Automated cost savings
Itron has also established better data acquisition and storage along with more reliable connection to SQL databases and other enterprise level services. Itron has always accessed roughly the same amount of data, but can now do it 15-20% faster in terms of the overall cycle time of the process using the Beckhoff system.

The time spent developing the software and the machine integration has also been drastically reduced. In the previous control system design with five pieces of control hardware, it took Itron as much as five times longer for programming compared to today when writing code for one multi-tasking piece of equipment. “We are literally savings weeks of engineering time – software, electrical and mechanical – for every new system we bring online,” said Moyer. When Itron duplicates these efforts on machines 10 or more times, the savings increase exponentially every time.
Measurable improvements to plant floor space and the assembly cell footprint also continue as a result of Beckhoff hardware and software integration. Cabinet space has reduced by an impressive 25%, which generates significant equipment savings on each assembly cell. System reliability and throughput have also improved using PC-based control and EtherCAT. With all of control functions and HMI integrated into one system, downtime has been reduced by at least 5%. “This is significant for an already high-performing facility because we have much faster startup through TwinCAT and EtherCAT connectivity as well as far fewer potential points of failure through the successful control hardware reductions,” noted Moyer.
All things considered, Itron has already tallied impressive results using PC-based control and today, Beckhoff automates approximately 35% of Itron’s factory. With the company’s position at the forefront of PC-based assembly technology, Itron can capably respond to each inevitable increase in product demand.
Are you ready to boost your assembly operations with PC-based automation and EtherCAT? Contact your local Beckhoff sales engineer today.

Shane Novacek is the Marketing Communications Manager for Beckhoff Automation LLC.
A version of this article previously appeared in Control Engineering.
Comments