How to Build a Better Rat Trap – with 70 Synchronized Servo Axes
- Matt Prellwitz
- Aug 15, 2023
- 4 min read
Updated: Aug 30, 2023
Using PC-based control and EtherCAT tech from Beckhoff, one Spanish system integrator delivered a sophisticated, highly efficient production line to enhance production for a major pest control brand
People often fixate on how to build a better mousetrap. An equally important pursuit, according to systems integrator Mitec Enginy, is figuring out how to build a mousetrap better. And combining both goals, the dynamic automation experts based in northern Spain have developed a sophisticated manufacturing system to produce traps for household pests.
The machine’s core element is a revolutionary motion control system with a total of 67 servo axes synchronized by camming function. The result is a production line that feeds, cuts, and bends wire, produces springs, and mass-produces the final product – a rat trap – in just 1.5 seconds. In addition to the servo drive technology, Beckhoff also supplies the required control performance with powerful PC-based control, EtherCAT networking and TwinCAT automation software solutions.
Mitec Enginy has been developing and integrating application-specific automation systems for customers around the world since 2006. The engineering company continuously focuses on innovation in the automation of industrial processes, the modernization of a wide variety of machines and the implementation of comprehensive solutions, according to Managing Director Albert Gratacos.

“We constantly strive to keep up with the latest technologies in order to offer our customers the most appropriate solutions for their automation problems,” Gratacos says. “Our close cooperation with Beckhoff is one of the most fundamental elements in this regard.”
Servo drive technology replaces mechanics
“Looking back at the history of automation, it is essential to appreciate the foundations that are simply taken for granted today,” Gratacos explains. “Eighty years ago, mechanically driven machines were quite common, often powered by a motor and connected by gears, crankshafts and cams. These inventions still drive our innovations today, yet these machines predate 3D CAD, CNC machining and software. With today’s technology, mechanical machine components are replaced by multi-axis servo movements and controlled more reliably and flexibly by software.”
The rat trap machine, as just the latest in many impressive applications from Mitec Enginy, showcases exactly this, according to Gratacos: “The customer needed to modernize their product manufacturing to remain competitive, so we devised an appropriate way to do that. At first, the idea of precisely synchronizing around 70 servo axes sounded almost crazy, but it ultimately proved to be the right solution for the complex process sequences, and we were able to implement it using PC-based control from Beckhoff.”
The system relies on 61 AX51xx and AX52xx servo drives paired with 67 AM80xx servomotors to power the various process steps. In terms of software, TwinCAT 3 with the camming function (TF5050 TwinCAT 3 NC Camming) ensures precisely synchronized motion sequences.
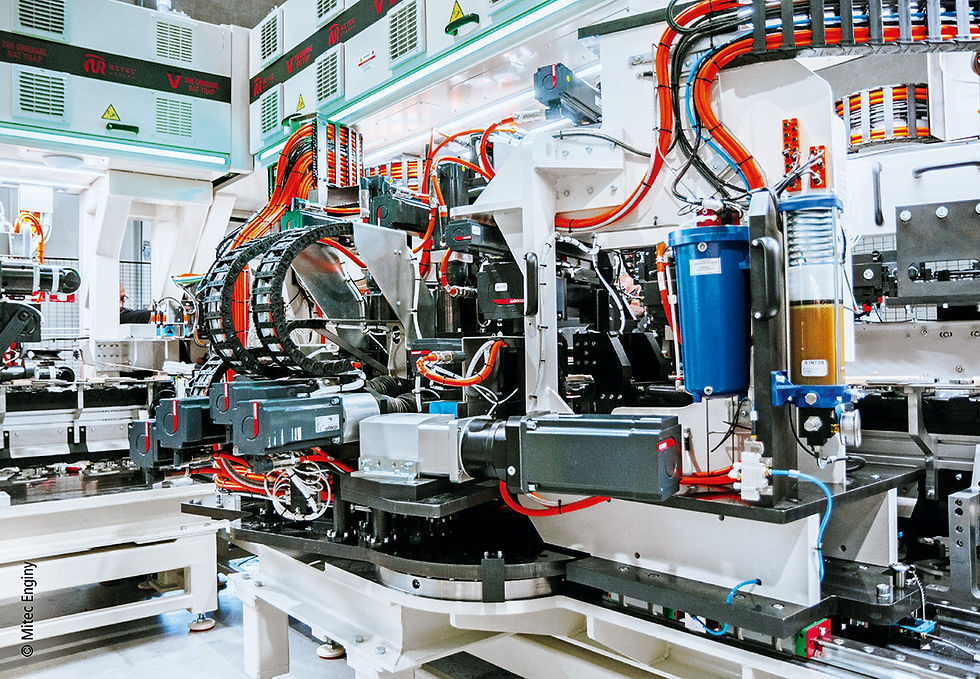
The EtherCAT industrial Ethernet system delivers optimal communication for motion control as a high-speed, high-bandwidth and extremely deterministic fieldbus. Ideal for all things motor- and drive-related, EtherCAT can handle the most basic PTP systems to advanced applications, like the Mitec Enginy machine. In addition, EtherCAT supports safe motion functionality. So, the rat trap machine implements all necessary safety functions (STO, SOS, SS1, and SS2) directly in the automation system with TwinSAFE and Safety over EtherCAT communication.
Just one PC-based machine controller can handle this expansive functionality. A Beckhoff CX2062 Embedded PC serves as the central controller, offering many-core processing power using advanced Intel® Xeon® processors. This delivered serious competitive advantages, according to Lluis Moreno, sales engineer at Beckhoff Spain.
“This is a very advanced machine featuring the latest automation technology,” Moreno adds. “It is fully equipped with powerful servo drive technology networked via EtherCAT and can be reliably coordinated with the CX2062 from just one computer.”
Complex solutions require a strong team
Mitec Enginy’s success can also be attributed to the team that has been created to develop complex automation solutions.
“We handle all of the mechanical and electrical design, programming and assembly of the automation in-house. At the same time, we recognize that no one person can be the expert for the entire automation system, which is why we have specialists in mechanics, electrics, and programming working closely together to develop innovative automation solutions,” Gratacos says. “But the team at Mitec Enginy doesn’t just stop with our employees; we also consider customers and suppliers like Beckhoff to be project partners and part of the Mitec team.”

Beckhoff also values intensive, trusting and long-term collaboration. That’s why we dedicate local engineering resources – from sales and applications experts in the field to training and support specialists at our offices – to ensure the success of customers around the world.
“Mitec Enginy is a long-standing partner of Beckhoff Spain,” Moreno says. “We have already implemented a number of very different and complex customer projects with them – often in a very special way. But I have to admit that the current production line is the most efficient and, dare I say, ‘beautiful’ machine in terms of design so far. Each of the many movements is just so fast, precise, and smooth that no unnecessary stresses are transferred to the mechanics of the machine.”
Interested in driving greater machine performance with high-precision servo technologies? Contact your local Beckhoff sales engineer today.

Matt Prellwitz is the Drive Technology Product Manager at Beckhoff Automation LLC.
A version of this article appeared in Machine Design.
Comentários