Smart Grid Implementation Enables Digitalization in Gas Management
- Jesse Hill
- Apr 4, 2024
- 4 min read
A Swiss operator deployed PC-based automation and intrinsically safe EtherCAT technology from Beckhoff for accurate monitoring of its natural gas supply network

Across western Switzerland, numerous stations that manage natural gas supplies are gradually being upgraded with new monitoring equipment. The company that operates these stations, Gaznat S.A., is working with Beckhoff Switzerland to achieve greater efficiency and accuracy, particularly by using ELX terminals for the direct connection of intrinsically safe field devices. In addition, this approach simplifies the processes required for data extraction, minimizes installation effort and considerably reduces costs.
Headquartered in Vevey, on the shores of Lake Geneva, Gaznat operates stations that perform gas depressurization. This essential process must be completed before natural gas can be safely forwarded to consumers. The stations reduce the gas pressure from approximately 38 bar to a value below the prescribed threshold of 5 bar. Subsequently, the natural gas flows to the local public utility, which then delivers it to area residents, other end users and industrial consumers.

Gaznat acts as an intermediary between the natural gas suppliers and municipal utilities and regional entities responsible for the local networks. Gaznat transports an annual energy equivalent of more than 13 TWh. The company's main task is to set up, maintain and operate the high-pressure transmission network in western Switzerland – some 600 km of gas pipelines as well as 50 pressure-reducing and metering stations.
Upgrading natural gas infrastructure in the age of digitalization
To secure, manage and remotely control its network, Gaznat requires digital and electronic solutions tailored to the technical specifics of its plants. The infrastructure of the stations includes substantial mechanical equipment, but is also equipped with state-of-the-art electronics, which is a prerequisite for digitalizing the gas supply network.
Just like electrical power grids, gas infrastructure is trending toward widespread adoption of smart grid systems and devices. In these applications, PC-based automation from Beckhoff offers an optimal platform for digitalization, according to Bertrand Luisier, Automation Manager at Gaznat. “It is a great advantage that Beckhoff can respond quickly to such specific customer requirements with its product development team,” Luisier says.
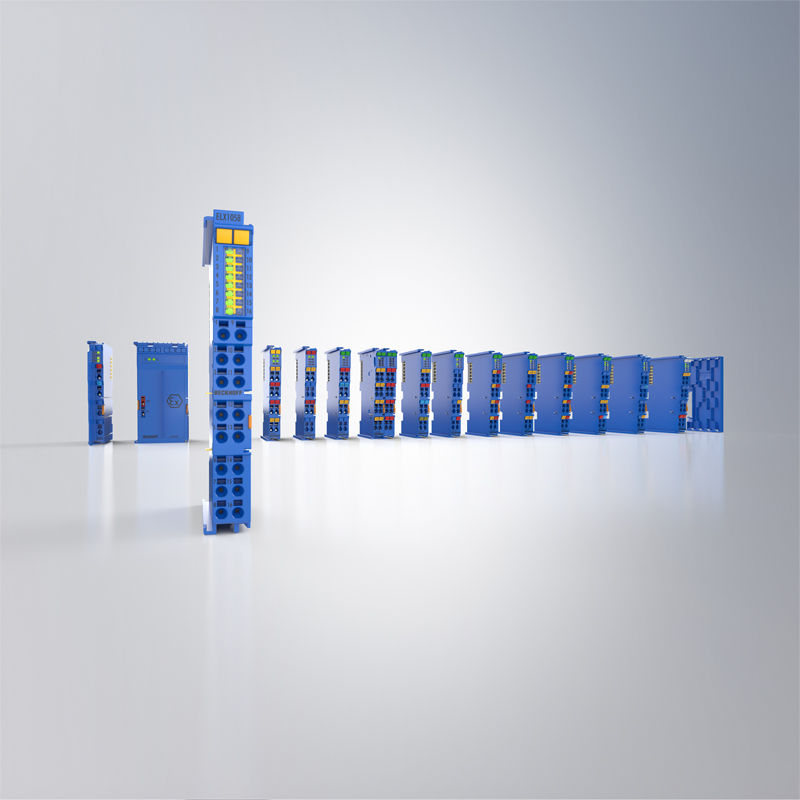
In the control cabinets of the gas pressure control system, the range of solutions from the automation company is evident in the wide range of EtherCAT I/O components, particularly the ELX terminals for applications needing explosion protection. The ELX range comprises digital and analog 12-mm and 24-mm terminals, respectively. These can directly acquire signals from field devices installed in station sections where gas flows.
This means that all data points within the plant can be connected directly to EtherCAT Terminals, both in hazardous and non-hazardous areas. This greatly simplifies overall installation and wiring, and intermediate devices such as intrinsically safe barriers or other signal converters are dispensed with completely. As a result of the large selection of EL series EtherCAT Terminals available, Gaznat found all the connectivity options it needed, such as:
monitoring power consumption with the EL3443 and SCT current transformers
lighting status in the station
control data for heating the gas
All this data is then transmitted via a Modbus I/O coupler to the control system for further processing. The solution delivers high flexibility, modularity and a comprehensive portfolio of EtherCAT Terminals for Gaznat to choose from.
Advantages of the intrinsically safe ELX1058
In the digitalization of these gas stations, the ELX1058 digital input terminal proved particularly useful, Luisier explains: “Beckhoff developed special firmware for us to use with the ELX1058 8-channel digital input terminal – for connecting intrinsically safe NAMUR field devices. This enables direct interfacing with a gas volume meter and dispenses with the device normally used for data acquisition from the sensor. Meter information is passed directly to the control system without the need for a serial interface, which was previously the case.”
As a standard module, the ELX1058 allows the direct connection of intrinsically safe NAMUR field devices installed in hazardous areas with zone 0/20 and 1/21 designations. The terminal acquires their signals according to the IEC 60947-5-6 standard. The module supplies the sensors with a voltage of 8.2 V and return a diagnosable current signal. So wire breakage and short-circuits can be detected in addition to the current switching state. The LEDs indicate the signal states as well as any error states.

On the software side, it is possible to define whether a positive or negative switching sensor is connected for each channel. Both NAMUR break contacts and make contacts can be integrated into the control system without any changes. In addition, the error LEDs can be switched off, which enables the connection of potential-free contacts without any errors being displayed.
EtherCAT fuels natural gas technology
In terms of economic efficiency, the use of EtherCAT Terminals from Beckhoff, and the ELX1058 in particular, leads to significant cost reductions, according to Gaznat. For example, retrofitted stations show savings of around 50% compared to conventional systems, which is equivalent to many thousands of Swiss francs. Troubleshooting is also simplified after the upgrades.
“Ultimately, this implementation, which provides a connection between station data and system monitoring by network operators, now requires fewer electronic devices because traditional safety barriers are no longer needed,” Luisier says. “In terms of space, everything now fits into one large control cabinet, whereas it used to take up two or three.”
Ready to harness digitalization in your process automation applications using intrinsically safe I/O? Contact your local Beckhoff sales engineer today.

Jesse Hill is the Process Industry Manager at Beckhoff Automation LLC
Comments