PostProcess Technologies, solutions provider for the Additive Manufacturing (AM) ecosystem, leverages PC-based control to revolutionize 3D printing industry
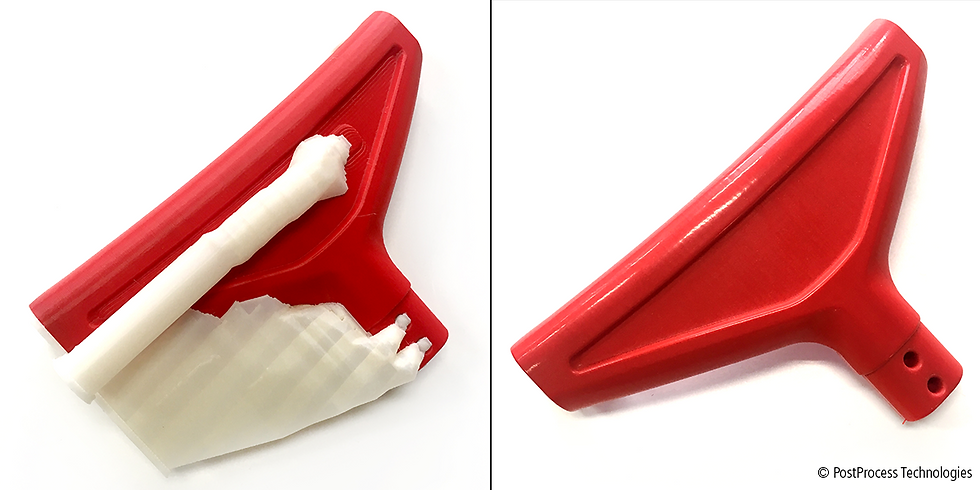
One of the greatest advances in manufacturing over the past few years has been 3D printing, also known as additive manufacturing. This is loosely defined as the process of creating objects from three-dimensional data by adding consecutive layers of material to copy a three-dimensional shape. A nearly infinite number of shapes can be created using 3D printing with all types of materials, including plastics, metals and even food. The process can also create shapes that would otherwise be problematic, if not impossible, to make without extensive multi-axis machining or highly specialized tools. Almost all manufacturers in the Fortune 100 and 500 are utilizing 3D printing to prototype parts. Direct digital production has also taken off to meet the needs for both low- and high-volume manufacturing applications.
However, the 3D printing process is not without its own set of challenges as part of the rapidly emerging field of direct digital manufacturing. Particularly when building complex geometries and materials via 3D printer, any overhangs or other asymmetrical contours require the use of support materials. These ensure that the workpiece does not collapse during production and they maintain the correct shape of the part during printing. The support materials must be removed afterward, creating inefficiencies. In addition, the 3D printing process can still be somewhat imprecise in general. The printed parts often require finishing to achieve the desired look and feel of a completed part while meeting tolerances for size, texture and precision.

Historically, skilled artisans performed post building processes by hand, requiring a high level of skill and unacceptably slowing the production process. PostProcess Technologies, on the other hand, had a more efficient idea – innovate by applying the same attention to detail using automation to expedite the finishing process. PostProcess founder and current President and CTO Daniel J. Hutchinson did just that, building on his extensive software background to create what PostProcess calls their Agitation Algorithm™ (AGA). PostProcess implemented this software along with a series of patent-pending machines that leverage a groundbreaking chemistry of detergents and abrasive media that dramatically increase throughput during post-print processing of 3D parts.
“Our solutions combine hardware, software and chemistry in an unprecedented way, helping us provide the only automated, intelligent and comprehensive offering to handle post-printing of materials and geometries for additive parts – further accelerating the fourth industrial revolution, or Industrie 4.0,” said Jeff Mize, PostProcess Technologies CEO.
To achieve this complex technology transformation, PostProcess needed a trusted partner to assist with the automation equipment, and determined that Beckhoff Automation could provide the right mix of expertise and leading-edge products to complement the innovative software solutions already designed by the company.
Finishing the job 3D printers started
PostProcess Technologies, a “Startup NY” designated company headquartered in Buffalo, was founded in 2013 with a vision – to revolutionize additive manufacturing by removing the post-print bottleneck. Today, the company has made good on this vision – partnering with Keller Technology, a global custom manufacturer, as their manufacturing partner PostProcess has established a line of automated finishing machines for 3D printed parts. This achievement represents a truly unique and previously unknown proposition in the additive manufacturing arena. The newest addition to their standard product offering is the Hybrid DECI Duo. This machine provides automated removal of support material and surface finishing in a single, multi-functioning system, all designed within a space-saving footprint that optimizes production floor space.

At its most fundamental level, the DECI Duo utilizes a combination of optimized energy from chemistry, guided by patent-pending Agitation Algorithms™ (AGA) to remove support material and provide the desired surface finish while preserving fine-detail part geometries. The DECI Duo was engineered for support material removal and surface finishing in the same footprint for a range of applications, including advanced thermoplastics, light-cured resins and metals.
Though PostProcess manufactures automated hardware for 3D manufacturing facilities, at their core they are first and foremost a software company. “The AUTOMAT3D® software we created to support the finishing process is truly the heart of what we do at PostProcess. Our innovative machines are the first of their kind, but the biggest differentiator for our company is in the software and our culture that supports post-print processing customers,” said Hugh McNeill, software development engineer.
One of the biggest benefits is that the machines do not require calibration for each individual part. The proprietary AUTOMAT3D software, which is powered by the Agitation Algorithms, allows for different agitation levels that cater to a variety of unique geometries, enabling customers to mix geometries into batches to save time and operate more efficiently. Precision and accuracy are also key to the process, as Michael Frauens, principal process development engineer explains: “Damage to parts while being finished is simply not an option. Often, these parts cost tens of thousands of dollars and may have taken weeks or even months to design and build. This highlights the importance of our AUTOMAT3D software; this revolutionary technology accurately inspects and interprets each part – regardless of geometry. In this way, we can provide reliable support removal and dependable surface finishing, producing ‘customer-ready’ parts, every time.”
Automation and IT convergence – the answer to 3D printing challenges

As PostProcess began R&D for their technologies, they knew they needed proven, robust automation components to complement the company’s advanced software solutions. Through their research, PostProcess determined that a full-featured PC-based control system from Beckhoff offered the best combination of price and performance for their needs. Hutchinson explains: “We felt that a PC-based control system would add an ideal level of familiarity for our customers. Since most of the 3D printers are not PLC driven, but rather PC driven, a familiar platform goes a long way to shorten the learning curve.”
To this end, PostProcess chose a Beckhoff CP6706 Panel PC with a 7-inch touchscreen and multi-core Intel® Atom™ processor (4 Core) to serve as the all-in-one control and HMI device for the DECI Duo system. The CP6706 offers exceptional build quality, with an aluminum bezel at the front and a sheet steel cover at the back. “We chose the CP6706 for a number of reasons. It checked all the boxes in terms of performance, and provided an aesthetically-pleasing look and feel that matched that of the machine,” according to Hutchinson. He also noted that the ability to communicate between separate devices, external sources and applications was a big selling point, as was the Windows 10 IoT operating system (OS).
“A PC-based platform that combines Windows OS and automation tools based in Visual Studio® was an ideal fit for our programming efforts, given that we are not specifically controls engineers, but lean more toward computer science. This convergence of automation technology and information technology as driven by Beckhoff enables us to have greater flexibility with our workforce, drawing from many different pools of engineering talent,” said Hutchinson.

TwinCAT 3 software from Beckhoff serves as the back-end for the DECI Duo system, providing real-time automation of the part processing operations. PostProcess implements several TwinCAT 3 runtimes on the CP6706 Panel PCs, including the TwinCAT PLC and 10 axis NC/PTP options. “TwinCAT 3, and in particular its integration with Visual Studio, is huge for us. We use Visual Studio Team Services for our configuration management, so the availability of industry-wide standards is especially beneficial. In addition, the ability to test the software on a virtual machine has helped substantially reduce our integration time,” said Dan Wascak, controls development engineer.
PostProcess has also standardized on a motion system from Beckhoff. A selection of AM8000 series servomotors with One Cable Technology (OCT) and several AX5103 EtherCAT servo drives offers a robust, space-saving motion solution. Hutchinson continues: “The AM8000 series motors fit our needs perfectly. Compact size and minimized cabling were at the top of our list of requirements, and these motors hit all the right marks. Pairing these with the AX5000 servo drives was an easy decision, as the combination of the OCT motors and EtherCAT as the drives bus made commissioning very simple.”
EtherCAT communication not only helps speed implementation of the motion system, it provides a complete system bus in the Hybrid DECI Duo, as Hutchinson explains: “EtherCAT is our sole communication protocol for all of the PostProcess Production series machines. The microsecond-level communication speeds and updates are unparalleled, enabling seamless scalability, multiple communication topologies, and the flexibility to use third-party hardware whenever needed, without compromising the network speeds.”
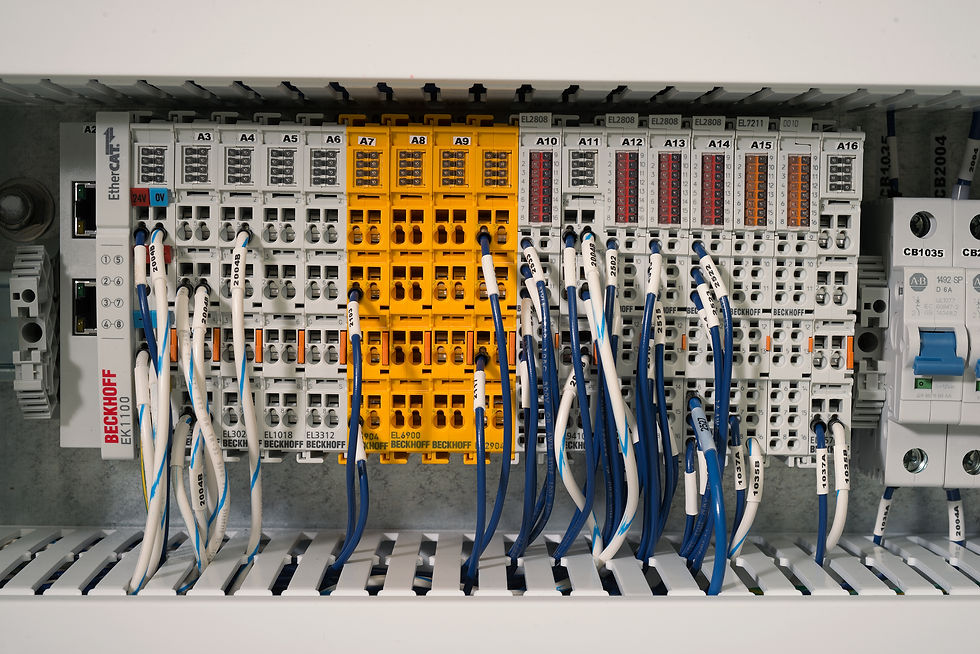
EL series EtherCAT I/O terminals from Beckhoff are installed across all PostProcess production lines. According to Hutchinson, “this provides maximum performance with a minimal footprint, and streamlines future efforts to integrate control of multiple machines.” PostProcess has also integrated safety technology using TwinSAFE I/O technology in the EtherCAT system. Special safety equipment such as e-stops and guard doors are easily connected via TwinSAFE I/O terminals.
Reduced programming time and costs are part of the winning process
Reduction in development time was the most important benefit realized by PostProcess upon implementation of PC-based control and EtherCAT. “With the Beckhoff system, our development time was cut in half,” reported Marc Farfaglia, Engineering Manager. “Much of this is due to the flexibility of TwinCAT 3 software and the ability to reuse function blocks and other code on subsequent machines. The PC-based system enables us to easily transfer code and have machines running in a minimal amount of time.”
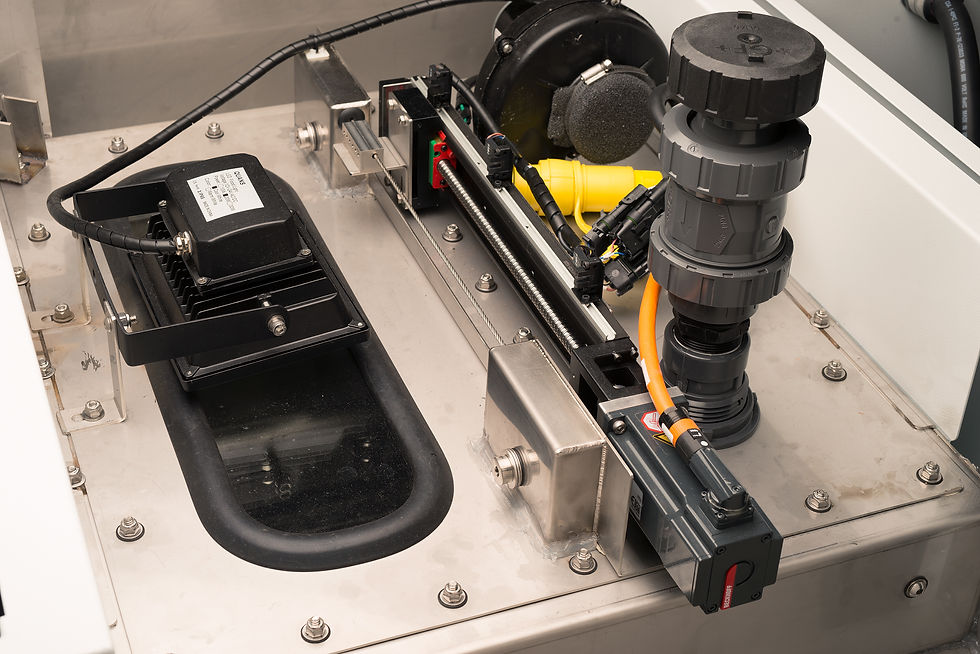
TwinCAT also provides a further benefit to the team at PostProcess, as the open and flexible software pairs very well with the AUTOMAT3D software. Hutchinson continues: “The ability to utilize industry standard development tools and configuration management services, such as Visual Studio, Visual Studio Team Services and 3rd party extensions greatly improves the development time, organization and learning curve for our developers.”
He noted that during development, the software-only simulation mode allowed PostProcess to significantly lower their hardware and software integration time. Hutchinson also praised the TwinCAT licensing structure implemented by Beckhoff: “The licensing strategy for TwinCAT enables us to efficiently and cost-effectively deploy any number of systems of any size. This empowers our engineers to quickly design, configure and develop without the headaches experienced with traditional licensing structures from other vendors.”
As the 3D printing and additive manufacturing market continues to evolve at a rapid clip, it is exactly this level of flexibility that will help OEMs like PostProcess shape the future of the industry.
Ready to take your additive manufacturing equipment to the next level with PC-based control? Contact your local Beckhoff sales engineer today.

Shane Novacek is the Marketing Communications Manager for Beckhoff Automation LLC.
A version of this article previously appeared in Design World.
Comments