The Revolutionary Benefits of XTS – Streamlining Engineering and Production
- Jeff Johnson
- Jan 25, 2024
- 5 min read
Updated: Jan 29, 2024
The modular linear transport system from Beckhoff enables footprint reductions up to 50% and changeovers on the fly and helps OEMs and manufactures implement IIoT and Industrie 4.0 concepts
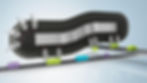
The space-saving capabilities of the eXtended Transport System (XTS) from Beckhoff come from the system’s extreme flexibility and modularity. XTS doesn’t simply offer a high-tech replacement for rotary index tables or conveying systems; it provides an opportunity for mechanical and controls engineers to fundamentally rethink product transport in their machine designs. The benefits of linear and continuous rotary motion, along with asynchronous movement of multiple movers, are available at the same time in the mechatronic system.
The system moves passive, wireless movers with high accuracy and dynamics using customizable rails and motor modules, with options for straight segments as well as +/-22.5, 45 and 180-degree modules. This leads to nearly unlimited geometries, including circles, ovals and S-curves, with movers traveling along the outside or inside of a track, depending on the design and requirements. Perhaps most importantly, XTS can be installed horizontally, vertically or at angles, increasing potential space savings through greater flexibility.
Beyond greater system flexibility, implementing XTS leads to fewer components on the machine and in electrical cabinets. As engineers rethink machine designs, they should be able to eliminate chain drives, actuators, rotary index tables and other expensive and space-consuming components that were previously necessary to accomplish these applications.
The XTS mechanical components and motor modules are relatively flat, and all power electronics are directly integrated into the motor modules. This mechatronic system eliminates the requirement for separate drive electronics or amplifiers that would increase footprint elsewhere. Real-world applications with multiple customers have repeatedly shown that footprint reductions of 25-50% are possible through proactive design and the advantages of XTS.
A modular system for flexible industrial automation
Modularity is a strong suit of the XTS, and it helps manufacturers and machine builder OEMs across industries implement Industrie 4.0 and IIoT concepts. The motor modules plug directly into each other and require just one Ethernet cable every 3 m to connect to the EtherCAT master. Guide rail options include the standard Beckhoff track for lighter payloads, which mounts to the side of the motor module, as well as integrated heavy-duty solutions.
HepcoMotion’s GFX Hepco Guidance System, for example, is a flush-mounted track that carries up to 12-kg loads. (Hepco GFX equipment is available in the U.S. from Bishop-Wisecarver.) There are a variety of mover options as well, depending on track and payload requirements. No matter the size, movers are always mapped as individual servo axes in TwinCAT 3 automation software, with built-in collision avoidance, jerk avoidance and automatic buffering. The three modular components combine to create nearly limitless opportunities for product transport.
While the motor modules, rails and movers enable designs with the utmost flexibility, the key benefit of XTS is that it supports easy reconfiguration without needing to be taken apart and reassembled. Program changes can happen on the fly, and in cloud-connected smart factories, machine builder OEMs or offsite engineering staff can perform updates remotely. The incredible modularity and customization of the system allows for rapid changeovers, enabling flexible mass production down to lot size 1. It’s truly a revolutionary way to approach machine design.
The benefits of streamlining engineering and production
The eXtended Transport System (XTS) from Beckhoff reduces the difficulty in setting up the system without reducing its capabilities. Compared to competitive linear transport systems, XTS offers a simplified approach in software and from a mechanical perspective, with fewer components and greater flexibility. The mechatronic system uses the same TwinCAT 3 automation software and EtherCAT network as the standard machine control, which further simplifies operation and doesn’t require engineers to learn an entirely new platform.
The TwinCAT 3 motion control library offers a wide range of preprogrammed functions for XTS, such as point to point, NC and flying saw. The universal engineering environment integrated into Microsoft Visual Studio enables intuitive programming via IEC 61131-3 languages and computer science standards. However, both controls and mechanical engineers must work together from the start when designing machines with XTS.
The key to successful implementation is considering how many functions the linear transport system can replace on the machine, rather than simply trying to substitute it for a low-cost conveyor. Although the movers are passive, they can handle a wide range of functions alone or in groups, such as clamping, opening bags at filling stations and rotating bottles with added tooling. The real-time communication of EtherCAT also allows XTS to work in concert with other technologies, including additional linear transport tracks, pick-and-place robots and other kinematics. For example, XTS tracks stacked on top of each other can propel movers simultaneously to carry the top and bottom of a part or complete another motion.
In addition, new XTS Track Management software enables physical adaptations to the track in real-time. Without losing functionality during the transition, motor module segments and movers can transfer between XTS systems with the addition of a spindle axis or linear motor. Track Management capabilities allow manufacturers to sort specific products out of the main production line, whether for additional customization, quality control inspection or simply clearing defective items. Eventually, it will allow work pieces to transfer between massive lengths of track and move throughout entire factories for any number of customization or other processes, helping manufacturers to implement and enhance Industrie 4.0 and IIoT concepts.
Forward thinking and customer requirements drive Beckhoff innovation
Every Beckhoff innovation is designed to meet both current and future needs of our customers, and XTS is no exception. The mechatronic system is perfectly suited to improve countless machine designs, and it has already proven itself in more than 1,200 real-world applications as diverse as assembly, bag filling, inline package assembly, product stream sortation and synchronization, and automated inspection using machine vision systems.
Another benefit of XTS is its greater track-and-trace capabilities; mapping each mover as an individual servo axis means that systems never lose track of the product. In addition, a stainless steel version of the XTS track and movers is planned for release in the near future for hygienic, wash-down environments. Both of these advances are important for our customers in many industries, but especially pharmaceutical, food and beverage.
For any manufacturing, packaging or processing operation, downtime is the primary enemy. Changeovers, in particular, create significant barriers to maintaining high throughput. But as Industrie 4.0 and IIoT concepts become more widespread due to consumer demands for greater customization and personalization, changeovers are becoming more, not less, frequent and necessary.
Through the implementation of a modular mechatronic transport system in place of inflexible mechanical components, manufacturers can meet these challenges by eliminating downtime for changeovers and enabling asynchronous processing. XTS also minimizes maintenance time through the benefits of direct drive technology, such as resistance to wear, low vibration and high energy efficiency. As a result, the linear transport system from Beckhoff provides significant savings through lower production costs and increased throughput.
Want to learn more about mechatronics can boost industrial automation applications? Contact your local Beckhoff sales engineer today.

Jeff Johnson is the Mechatronics Product Manager for Beckhoff Automation LLC.