There Is No One-size-fits-all IIoT Strategy — Part 2
- Mark Ruberg
- Dec 28, 2020
- 3 min read
Updated: Jul 19, 2023
What really is IIoT and how can it be successfully implemented in the packaging industry?
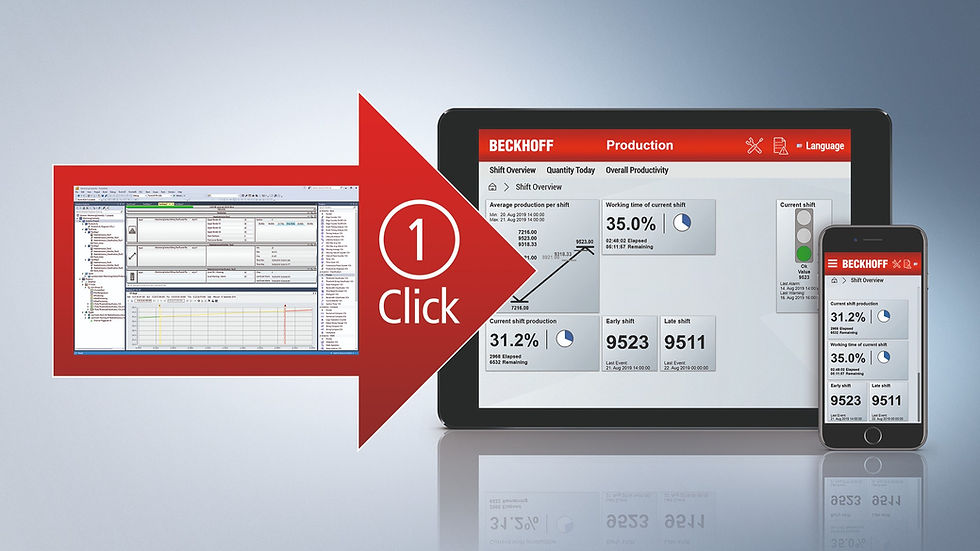
Dating to early Internet of Things (IoT) implementations — a Carnegie Mellon University vending machine retrofitted with a sensor and communicating over ARPANET in 1970 is often recognized as the first — the idea has remained relatively consistent. IoT simply involves connecting machines and components via a telecommunications infrastructure back to centralized computers with the ability to manipulate and monitor those machines remotely. Now, in the age of cloud computing and big data, the use of IoT for manufacturing has become conflated with sending all data to a third-party cloud. As a result, IT and OT departments at companies have fought about how to gather, store and leverage information.
IIoT can certainly include a cloud-connected strategy, with real-time machine learning and analytics tools to optimize OEE. This strategy is a good fit for large, multi-site operations and could be beneficial for smaller packaging machine OEMs and CPG manufacturers, too. However, IIoT could also include aggregating data at the enterprise level, sending compressed binary files for review in analytics software or performing analytics on the machine controller during production.
Sometimes engineering and plant management don’t want to connect machines to the cloud for various reasons. Some don’t even want to connect machines to horizontal machine-to-machine (M2M) networks, leaving them true islands of automation. While this is often due to resistance to change, there can be valid security reasons as well. But vendors shouldn’t leave engineers stranded in these instances, and should offer solutions that provide IIoT advantages at any level.
Choose the right platform for IIoT
IIoT strategies are not one-size-fits-all, so companies should look for a platform that accommodates significant customization. PC-based automation offers a universal platform for both machine control logic and effective use of all connected assets. The programming environment in TwinCAT 3 automation software from Beckhoff, for example, is fully integrated into Microsoft Visual Studio®. This allows controls engineers to build IIoT projects in programming languages they are already familiar with, so companies don’t need to hire outside programmers or purchase expensive third-party software. TwinCAT 3 also supports the use of numerous computer science programming languages in the same projects if desired.
Platforms should support common IIoT project requirements with advanced analytics packages. TwinCAT, for example, now offers one-click dashboard creation for faster viewing of OEE information without starting from scratch on a complex HMI program. In addition, communication options include the most current encrypted cloud communication protocols, such as OPC UA, AMQP and MQTT. TwinCAT also easily integrates with Microsoft Azure, Amazon Web Services (AWS) and other major cloud services. A built-in digital oscilloscope provides easier viewing of real-time data, and machine learning can make changes on the fly to automate production improvements without operator intervention. Unlike with traditional PLCs, this functionality can occur directly on the PC-based controller, removing the cost of installing and protecting a secondary computer on the plant floor.
Industrial PC (IPC) hardware for IIoT applications can connect directly to the cloud — with or without the addition of an auxiliary gateway, depending on plant requirements. The IPC could serve as an edge computing device to process data and make decisions in real time before sending relevant data to the cloud for further analysis. For islands of automation, IPCs can still run advanced analytics or machine learning on board, and then maintenance staff can export and analyze data intermittently. The range of Beckhoff IPCs is well suited to these tasks, with devices officially certified for both AWS and Azure. However, a smaller application could be as simple as a DIN rail-mounted IoT coupler that integrates into an existing EtherCAT I/O segment.
Start small and grow from there
For many small packaging operations or machine builder OEMs, it helps to start small. An IIoT project doesn’t have to be a multi-million-dollar plant upgrade or a trip into the Matrix. In the case of monitoring compressed air, for example, it could be the addition of one or more air sensors that communicate to the PC-based machine controller or gateway device. This would allow a company to send alarms to maintenance, create useful dashboards to monitor performance and analyze data for performance enhancements. These are all possible without giant capital investments.
Wherever you plan to start, make sure your technology platform offers scalability for the future. After all, IIoT may seem like a buzzword now, but the technology will only continue to grow.
Want to learn more about applying IIoT technologies to your packaging operation? Contact your local Beckhoff sales engineer today.
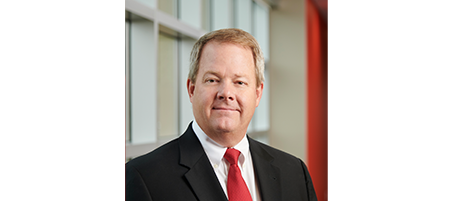
Mark Ruberg is the Packaging Industry Manager for Beckhoff Automation LLC.
A version of this article previously appeared in Packaging Strategies.
Comentários