Top 3 Advantages of Integrated Explosion Protection Functionality
- Jesse Hill
- Mar 30, 2021
- 4 min read
Updated: Jul 19, 2023
With recent technology advances, intrinsic safety now offers the safest, most cost effective and easiest way to deploy solutions that safeguard your process operations
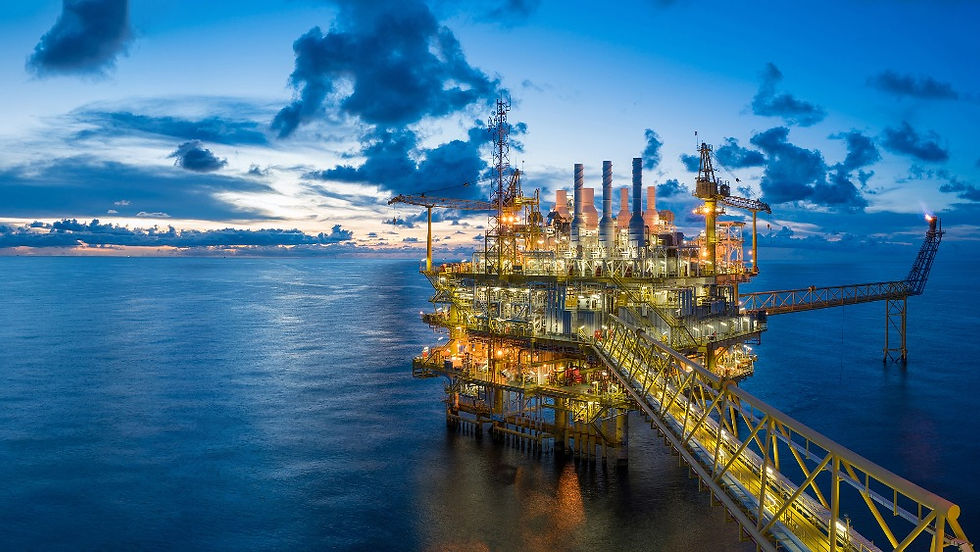
In every industry I can think of, exploding equipment is most certainly a bad thing. In process industry settings, however, the risk of explosions is very real. And the stakes – from impacts on revenue and the environment to loss of life – are far too great to ignore.
Engineers designing electrical equipment and processes for use in hazardous areas are offered a multitude of different methods for explosion protection. These range from exclusion methods, such oil immersion or purge and pressurization, to containment in the use of explosion-proof or flame-proof enclosures, as well as energy limiting technologies, such as non-incendive, increased safety or intrinsic safety. These principles and techniques have some inherent advantages and disadvantages. There are also some ideal applications, for example, protecting an entire control room using pressurization.
In the correct situation, however, intrinsic safety stands out as the safest, least expensive and easiest to deploy. Let’s examine why.
1. Intrinsic safety is the safest form of explosion protection
First, intrinsic safety is the only method of explosion protection approved for Zone 0. This is the most hazardous area recognized by ATEX, IECEx and NEC (article 505) and is considered hazardous “continuously.” The reason for this is that intrinsic safety is required to withstand two electrical faults and remain safe. It is also immune to some of the issues arising from mechanical explosion-proof installations, such as improperly sealed conduits and damaged or improperly secured enclosures. In additional to superior safety from explosions, intrinsic safety is also inherently safer for personnel as its energy limiting principle typically only allows for up to 30 V or 100 mA to the hazardous area.
2. Intrinsic safety is the least expensive way implement explosion protection
In many cases, non-hazardous rated equipment can be used in an intrinsically safe circuit if it meets certain criteria. These devices are considered “simple apparatuses,” which means they are not capable of generating more than 1.5V, 100mA or 1.5 W or they dissipate more than 2.5 W. These devices include thermocouples, switches, RTDs and LEDs and are typically much less expensive and more readily available than hazardous area approved devices.
Another area in which intrinsic safety is less costly than other forms of explosion protection is the ongoing maintenance of the process or machine. Since they use energy limitation as an explosion protection concept, the devices in the hazardous area can be worked on without removing power. Additionally, maintenance time and effort can be significantly reduced because no gas clearance is required, and additional time is no longer needed to access electronics inside explosion-proof enclosures.
3. Intrinsic safety is the easiest explosion protection method to deploy
One of the biggest deployment advantages to intrinsic safety is the ability to use mostly safe area wiring practices. Of course, there are some wiring rules to follow, i.e., intrinsically safe and non-intrinsically safe wiring must be separated by 50 mm, and intrinsically safe wiring must be identified by a label or light blue cable jacket. However, all other aspects of wiring – when to use cable tray, types of glands, etc. – are similar to safe area wiring practices. This is in comparison to the multitude of rules regarding explosion-proof wiring installations, such as how and where conduit must be sealed as well as the type of cables and fittings required by the electrical codes. Intrinsic safety is also much easier to deploy than purge or pressurization systems as there is no need for a supply of inert gas to pressurize the enclosure nor the tubing and fittings associated with this gas supply.

Exciting technological advancements in intrinsic safety technology are making these deployments even simpler. An example is the integrated intrinsic safety in the ELX series EtherCAT Terminals from Beckhoff. These components combine explosion protection with a standard, DIN-rail-mounted I/O terminal. Other vendors offer some sort of integrated approach to explosion protection, but many result in different form factors than their non-ex counterparts and they cannot be integrated directly into the same I/O node with non-ex terminals.
The ELX approach provides many other benefits. For starters, it eliminates the need for a third-party intrinsic safety barrier. This not only greatly reduces the size of the enclosure that houses the control system, but it also cuts the number of time-consuming wiring terminations in half. This also eliminates the need to add another vendor to the bill of materials. Another noteworthy benefit of the Beckhoff ELX system is that customers can take advantages of all the benefits of EtherCAT technology, including:
Real-time communication speeds at 100 Mbit/s and the EtherCAT G/G10 Gigabit expansions that will soon offer even greater bandwidth for demanding applications
Free selection of topology without any impact on performance
Practically no network size limitations, with up to 65,535 nodes on a single EtherCAT network
High synchronization due to the principle of distributed clocks
Make your applications intrinsically safe today
In terms of safety, cost and ease of deployment, the benefits of intrinsic safety are clear, and technology I/O advances like the Beckhoff ELX series make this even more obvious. Engineers should evaluate whether this method fits their application and implement it as appropriate. It’s also important to work with technology partners that take the risks just as seriously as you do and provide solutions to help keep your team, company and equipment safe.
Are you interested in implementing intrinsic safety in your process applications? Contact your local Beckhoff sales engineer today.

Jesse Hill is the Process Industry Manager for Beckhoff Automation LLC.
Comments