TwinCAT/BSD Bridges the AT-IT Divide in Intralogistics
- Casey Taylor
- Mar 13, 2023
- 5 min read
Updated: Jun 26, 2023
Machine controllers using the Windows-alternative OS and accompanying Hypervisor boost security and edge computing capabilities in industrial control systems
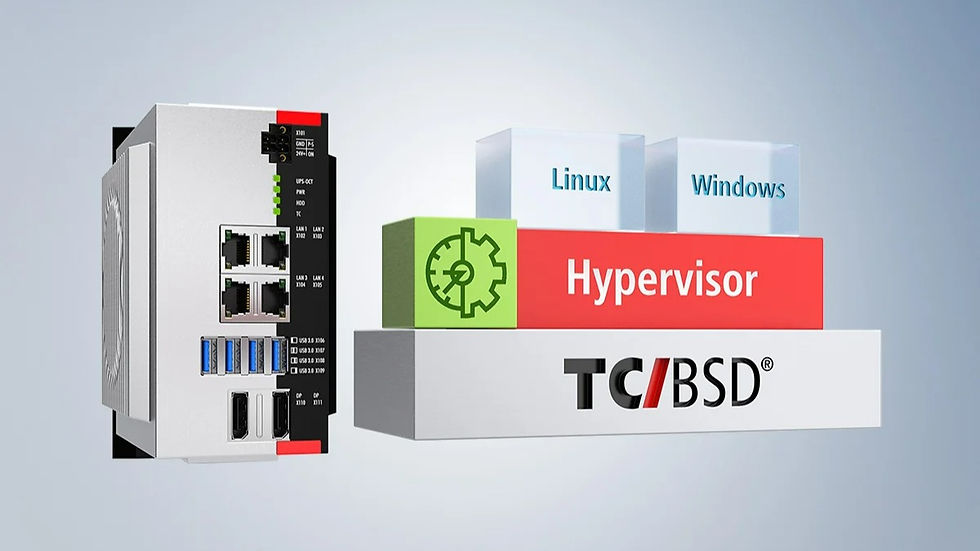
Here’s an all-too-common scenario: Autonomous mobile robots (AMRs) and automated guided vehicles (AGVs) need to cram navigation, vision, lidar, battery, PLC and safety functionality into an incredibly compact enclosure. But the black box technologies that AGV makers normally use simply will not fit inside.
These “typical” components introduce excessive space requirements, and reduce the life cycle of the overall control platform due to the separate CPU hardware and add unnecessary costs. That is the way it has always been done, so the idea that multiple functionalities could be combined onto a single piece of hardware may seem revolutionary. The convergence of AT (automation technology) and IT is just the starting point. But many managers in intralogistics operate under the misconception that PC-based control must run on Windows.
With the release of TwinCAT/BSD in 2020, Beckhoff has introduced an alternative operating system (OS) based on FreeBSD for our industrial machine controllers. This non-Windows solution works seamlessly on Beckhoff controllers and utilizes the same universal automation software platform for developing PLC projects, TwinCAT. The accompanying Hypervisor adds even more benefits like the ability to use multiple operating systems on one device via implementation of virtual machines.
Numerous applications have already proven the power of TwinCAT/BSD in the field. Customers have also commended the ease of porting existing TwinCAT projects from a Windows-based system to TwinCAT/BSD without hardware or software changes.
Even for companies where Windows is accepted, benefits like smaller OS image size for faster deployment and lower licensing requirements have proven beneficial. Additional OS features include write filters similar to legacy Windows CE as well as snapshots, replication and snapshot cloning, all with support of ZFS (previously Zettabyte File System), which is a powerful volume manager and file system that also protects data stored on the device and the OS from corruption. Most importantly, machine controllers running TwinCAT/BSD do not lose anything compared to the traditional Beckhoff solution; even robust graphics support is included.
Like a PLC except better
With the alternative OS, the Beckhoff controller acts even more like a modern PLC in its designed architecture. It continues to take advantage of processors from Intel, AMD, ARM and more but with greater performance, openness and functionality than other PLCs on the market. Current PLCs, after all, do not use the proprietary firmware of yesteryear. Practically every PLC vendor uses Intel or Arm processors and a commercially available real-time operating system (RTOS), or third-party real-time kernel. The difference is: It locks you out. The engineers have less visibility and less freedom as a result.

TwinCAT/BSD mirrors this by using FreeBSD, a Unix-compatible open-source operating system directly originating from Berkeley Software Distribution (BSD). As an open-source project, FreeBSD is continually being developed further, improved and optimized by a large group of developers. Unlike current PLCs, the Beckhoff approach increases long-term availability, reduces license costs and retains our decades of controller development expertise.
The standard Beckhoff architecture allows engineers to consolidate all functionality – from PLC and motion control to HMI, IoT and machine vision to robotics and mechatronics, even executing these functions synchronously – onto one powerful piece of hardware. Third-party software can also run on the controller. So in the example above, the mobile robot maker could shrink the hardware requirements to a single Embedded or Industrial PC (IPC) from Beckhoff and support all software functions of the AGV. The controls footprint could now work for the compact enclosure on AGVs, or much smaller AMRs, and save costs.
“The power and flexibility of TwinCAT/BSD with its Hypervisor creates countless new opportunities to innovate and secure a competitive edge.”
Beyond that, advanced Beckhoff features like our controllers’ core isolation capabilities for multi-core and many-core processors remain available with TwinCAT/BSD. This enables a quad-core controller, for example, to isolate the OS on Core 0, run one PLC program for machine control on Core 1, another for data analysis or machine learning on Core 2 and motion control or another machine function on Core 3 and so on. By isolating the OS from the PLC on another core, tasks are executed with minimal or zero jitter.
And with the hypervisor, commonly referred to as bhyve, you combine all this functionality with the ability to run virtual machines with other operating systems, such as Linux, QNX or Windows for instance, on a single machine controller. This opens the door to run virtually any software on the automation devices alongside the TwinCAT real-time control and PLC software.
The added benefit is that the OS and software executables can be updated in the virtual machines without having to restart the host OS that is handling the real-time machine control. As a result, you can deploy patches and other updates to Windows, or to another OS that is running user-level functions in the virtual machines without restarting the host OS and real-time kernel in TwinCAT/BSD. This enables successful installations of vital security patches without impacting machine operation.

The smart warehouse of tomorrow – today
The advantages of TwinCAT/BSD are clear even when communication, rather than footprint, is the top concern. With robust control hardware, this alternative OS enables intralogistics operations to start implementing the smart warehouses of tomorrow right now. Engineers can leverage TwinCAT IoT libraries to send orders from the cloud and performance data back for analysis or machine learning. At the field level, real-time EtherCAT communication delivers the extreme data throughput necessary. However, they can still harness the reliability and security of a modern Unix-like operating system and the extensive built-in cybersecurity features of EtherCAT.
Consider another scenario that’s of growing interest – complete fulfillment center digitization: A large fulfillment operation needs to implement equipment across its massive warehouses, and that equipment needs to talk to higher-level enterprise or cloud systems to give updates on OEE (overall equipment effectiveness). Typically, the warehouse operator will need to add a separate PC or edge device with local analytics algorithms and a separate network to manage all the data from sensors before sending the results to the enterprise level. This would multiply expenses, add points of failure, make update management a headache and, again, add obsolescence concerns.
A TwinCAT/BSD system, on the other hand, enables state-of-the-art industrial edge computing. EtherCAT already offers bandwidth for large amounts of data, eliminating the need to add parallel networks. And the standard Beckhoff machine controller natively supports the functions of both the PLC and the edge device, with capabilities for local data collection and local analytics. Running a Windows or Linux virtual machine in the Hypervisor, you could implement AWS IoT Greengrass or Azure IoT Edge directly on the machine controller.
Also supported is an additional way to deploy multiple, isolated services on a single Beckhoff controller via container technology, such as those offered by Docker or Kubernetes. Containers simplify packaging, deployment and management of lightweight applications. This has proven beneficial in advanced edge scenarios. The power and flexibility of TwinCAT/BSD with its Hypervisor creates countless new opportunities to innovate and secure a competitive edge.
Is this the end of Windows?
Not by a longshot. Beckhoff continues to see the value of Windows for our engineering environment in Microsoft Visual Studio®, and many applications still benefit from Microsoft’s continued Windows development and capabilities of that OS. However, TwinCAT/BSD offers a worthy alternative for applications where it makes sense or where the equipment end user simply will not allow a Windows-based machine controller.
Continued AT-IT convergence remains our goal. This alternative OS option brings the longstanding benefits of the fully integrated Beckhoff controls architecture to applications where it perhaps was once locked out due to different technology preferences in 24/7 distribution operations.
Extend system life cycles. Reduce CPU and other hardware requirements. Deliver advanced computing power. Introduce new possibilities for your intralogistics equipment with TwinCAT/BSD.
Done waiting for black box control solutions to provide greater performance and flexibility? Contact your local Beckhoff sales engineer today.

Casey Taylor is the Software Product Manager for Beckhoff Automation LLC.

Eric Reiner is the IPC Product Manager at Beckhoff Automation LLC.
Comments