With the Peakanalyzer, GfM provides high-end vibration analysis in wind turbines. These capabilities rely on PC-based control from Beckhoff.

Wind energy continues to grow at a rapid pace. In 2021, the global installed capacity for wind energy generation added 93.6 GW, bringing the total to 837 GW, according to the Global Wind Energy Council. Still more is needed. With the growing importance of this energy source, unplanned maintenance could cause the winds of fortune to change quickly for operators.
Tried and tested in wind turbines, the Peakanalyzer is a universal solution for fully automatic vibration diagnostics from Gesellschaft für Maschinendiagnose mbH (GfM). The system monitors the entire wind turbine drive train, and optionally the wind turbine foundations, reliably and with high precision. Berlin-based GfM specializes in vibration diagnostics for gear units mounted on roller bearings, according to Co-founder and Managing Director Dr. Rainer Wirth.
“Our research and development work has always focused on the automation of diagnostic processes, since this is the key for widespread acceptance of these technologies,” Wirth explains. “GfM actively promotes the combination of diagnostic services and device development, so that practical experience can directly feed into product development.”

One of the devices that has benefited from this approach is the Peakanalyzer, designed for fully automatic, high-end vibration diagnosis at up to 32 measuring points, with up to 32 further channels for slower process variables (1 kHz). At the heart is PC-based control technology and EL3632 EtherCAT Terminals for condition monitoring (IEPE) from Beckhoff.
This approach harnesses Scientific Automation concepts for integrating measuring functions that go beyond standard automation, such as condition monitoring. In this way, the Peakanalyzer enables many capabilities, including:
order analysis through resampling for diagnostics of variable-speed drives
DVS (Drive Vibration Significance) analysis for automatic identification of significant spectra
characteristic value monitoring
triggered data acquisition
Typical areas of application for this versatile diagnostic device are for costly, low-redundancy drives, such as in mills for the building materials industry, drives in conveyor systems – where availability is a critical requirement – or safety-relevant drives in cable cars, for example. The Peakanalyzer is also frequently used for drives that are difficult to access and for which condition-based maintenance is therefore a prerequisite. Wind turbines are a prime example of such applications.
Comprehensive condition monitoring for wind turbines
The eight-channel Peakanalyzer is ideal for monitoring wind turbine drive trains and can optionally also monitor the foundations via two further channels to detect loosening. The diagnostic device is installed in the wind turbine nacelle, either in the control cabinet or in a dedicated housing. The system analyzes the drive train based on the signals acquired by eight IEPE acceleration sensors: one sensor for the main bearing, two for the generator and five for the gear unit. If required, the Peakanalyzer can be integrated into the existing communication structure (LAN interfacing in the nacelle, VPN access), or communication can be established via wireless communication, fiber optics (tower) or via GHSDSL (copper cables between systems), as well as through DSL to the internet provider.
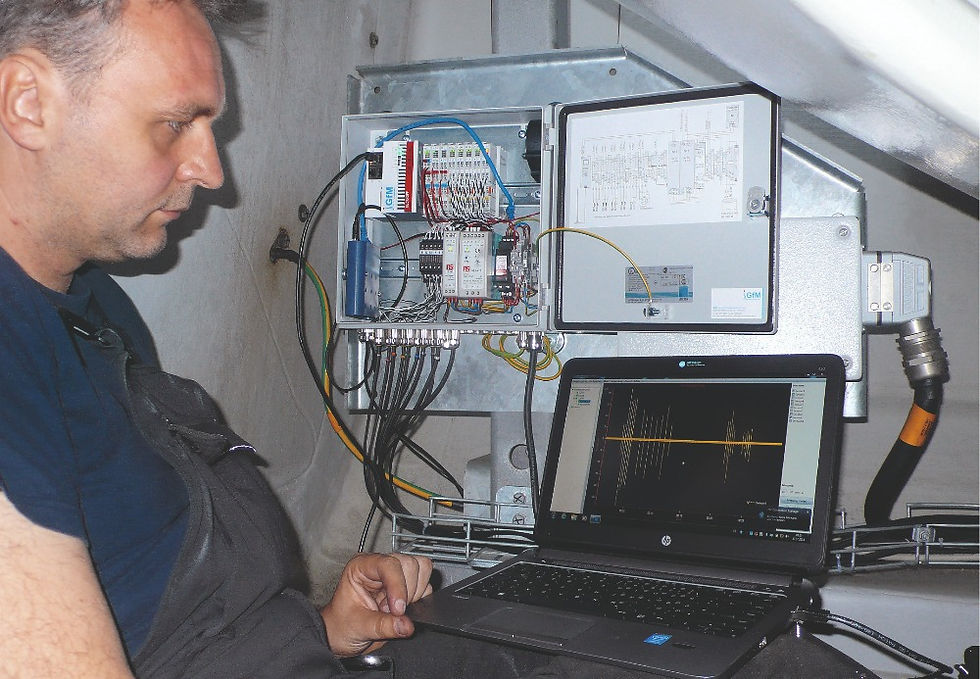
GfM software developer Christian Reinke explains the benefits of the underlying PC-based control technology: “The modular control technology from Beckhoff enables us to offer customized and cost-effective diagnostic solutions that are highly scalable, based on a freely programmable, open system, and with globally available and exchangeable spare parts, if required.
“What’s more, distributed solutions can be easily realized with the EtherCAT Terminal I/O system,” Reinke adds. “Based on the high-performance communication via EtherCAT, the Peakanalyzer can be offered with up to 32 input channels for enhanced application flexibility. Moreover, a high channel sampling rate even with lower bus cycles can be achieved based on the oversampling functionality of the EL3632 and EL3702 EtherCAT Terminals, and this is how the Peakanalyzer is able to support such accurate vibration recording and evaluation.”
A CX5000 series Embedded PC from Beckhoff performs measuring data acquisition and buffering based on TwinCAT automation software. The information is then passed via ADS (a communication protocol within TwinCAT) to GfM’s proprietary analysis software for further processing. Christian Reinke continues: “The advantage lies in the direct control of the PLC. That is, the communication is based on a universal PLC, so that different system configurations with different numbers of channels and terminal types only need to be distinguished in our software.”
Remote access is also possible. To this end, the GfM .NET application on the embedded PC communicates with configuration and evaluation software on the corresponding network computer via TCP/IP.
Condition monitoring terminals: essential I/O equipment
Sensor data for drive monitoring is logged with high precision via the two-channel EL3632 EtherCAT Terminals, an essential component of the Peakanalyzer, according to GfM co-founder and managing director Axel Haubold.
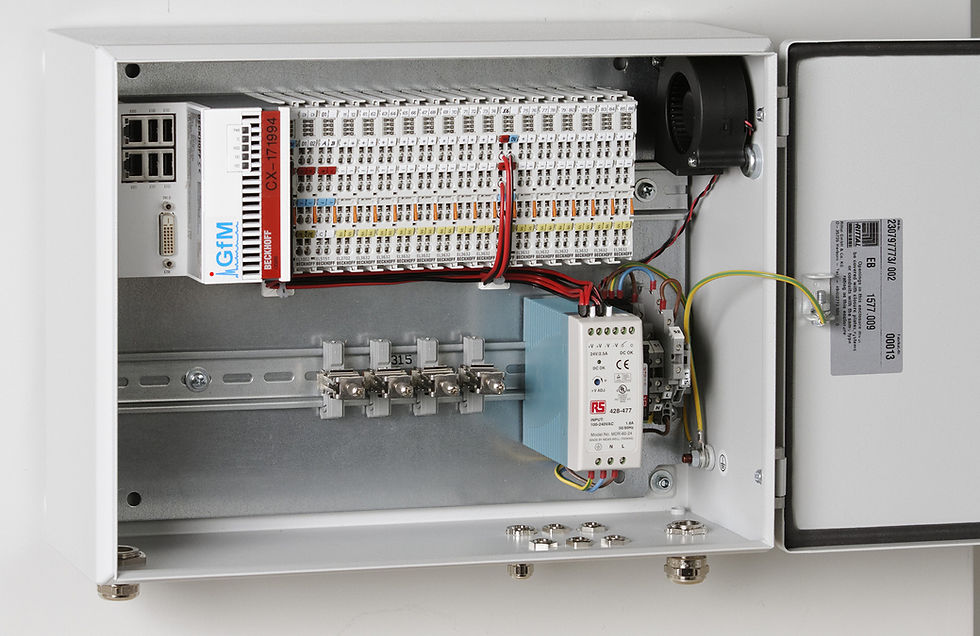
“The key for the implementation of our high-end vibration monitoring system is the acquisition of the IEPE sensor signals with a sampling rate of 50 kHz. An additional factor is the very wide sampling range between 1 Hz and 1 kHz, which enables the device to measure low-frequency vibrations (e.g. tower oscillations) and high-frequency vibrations (e.g. vibrations at the actual wind turbine) at the same time,” Haubold explains.
“In order to obtain a high-quality envelope signal for detecting roller bearing and gearing damage, all channels almost exclusively measure with a clock frequency of 50 kHz. Particularly in the wind industry, the 0.1 to 10 Hz mode is additionally used for logging characteristic values according to VDI 3834,” he adds. “A further benefit, particularly during commissioning, is the breakage detection feature offered by the EL3632 condition monitoring terminal.”
The Peakanalyzer’s I/O range can accommodate further interfaces to meet customer requirements, according to Reinke: “Here, we benefit from the wide range of solutions in the modular EtherCAT I/O system. For example, via pulse time measurement, the EL5151 incremental encoder interface enables very precise speed measurement with several, non-equidistant pulses per revolution. The EL3702 analog input terminal with oversampling is ideal for recording oscillation movements via inductive displacement sensors for monitoring slowly moving roller bearings.”
EL1002 digital input terminals are used for triggering measurements, and EL2004 digital output terminals handle the signaling of characteristic values and process parameter alarms. Important process variables such as power, wind and torque can be integrated in the diagnostic system as analog voltage signals (±10 V) or current signals (0 to 20 mA) via the EL3702 or EL3742 EtherCAT Terminals. In addition, EL3356-0010 eXtreme Fast Control (XFC) load cell analysis units are available for torque measuring points, and high-precision EL3202-0010 PT100 input terminals are available for temperature measurements.
Want to further safeguard your process industry equipment with integrated condition monitoring? Contact your local Beckhoff sales engineer today.

Jesse Hill is the Process Industry Manager for Beckhoff Automation LLC.
Comments