Modular Window Film Application System Reveals High Precision and Throughput
- James Figy
- Jul 7, 2022
- 7 min read
PDS IG Equipment doubles window film throughput compared to the industry standard using EtherCAT and PC-based control
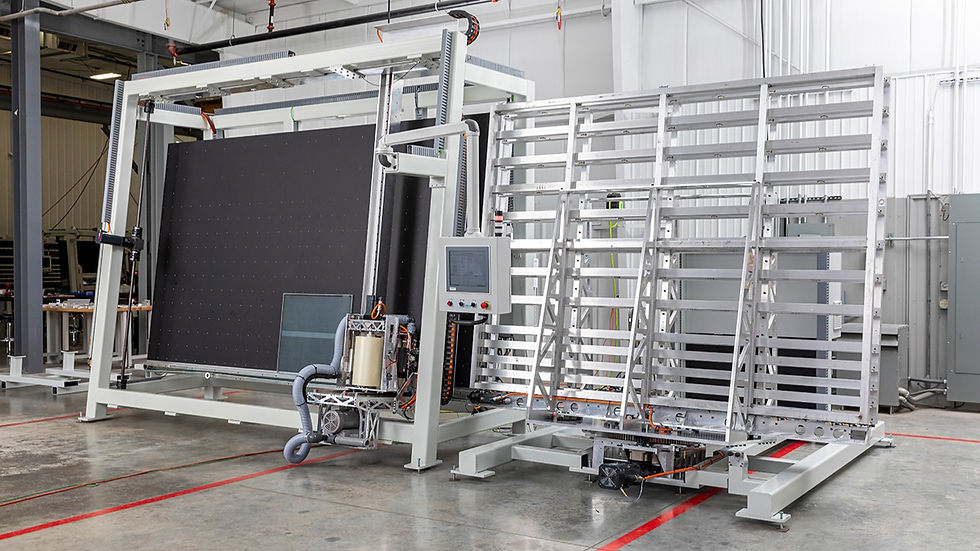
Under normal circumstances, windows in homes, offices and other buildings are not in great danger of damage, but that is not the case during installation. “During construction projects, glass windows face significant risks from splashing concrete, dirt, debris and other hazards, such as tradespeople carrying tools and materials,” says Michael Rapp, vice president of sales and part-owner of PDS IG Equipment. “Applying window film during the manufacturing process not only protects the window, but it also allows contractors to simply peel off anything that might have stuck to it.”
To ensure the polyester (PET) film is applied with high repeatability, short cycle times and robust data acquisition capabilities, PDS IG created a modular automated solution to protect insulating glass (IG) units of all sizes during manufacturing, shipping and installation.

The PDS IG Equipment technology portfolio includes a broad range of window production machinery, including equipment to install spacers for IG units. Based in Prairie du Sac, Wisconsin, the company was formed in 2011, after the success of Infinite Edge Technologies, which was founded in 2008 to focus on spacer technologies. “The company keeps growing. In recent years, we doubled our factory space to 60,000 square feet and added more than $1 million in new production equipment and infrastructure to meet demand,” Rapp says.
PDS IG built its window film application system after recognizing a lack of efficient automated systems for the process, which is nearly impossible to complete manually. Beyond offering high throughput, the modular machine design allowed greater control and flexibility for facilities operators and managers.
Sizing up film application system requirements
The PDS IG window film application system uses multiple modules, beginning with an intake conveyor module. Operators or robots carefully load glass onto the conveyor, which transports each piece into the film applicator module. During this process, the machine measures each insulating glass unit individually, according to Steve Polkinghorne, automation controls engineer at PDS IG. “The machine measures the length by taking a position latch of the rising edge and the falling edge as the units enter, and it uses a measurement sensor for the height,” he says. “Then while applying the film, the machine takes a high-speed snapshot of the unit’s position relative to the axis position to fine-tune all of the measurements.”

The application head covers the surface with as many passes as necessary using 12- to 16-inch rolls of PET film. Once film is applied on one side, the IG unit moves into a glass-flipping station that turns the workpiece 180 degrees horizontally and conveys it into the second film applicator to cover the other side. Finally, an operator or robot offloads the fully protected glass.
When PDS IG engineers began to design the system in early 2018, they knew that real-time communication was key to ensuring precision. The film applicator needed to leave a consistent “cutback.” This is a thin strip around the edges that remains uncovered, allowing the glass to be installed in the sash without film becoming stuck behind the frame.
“These windows range from 12 inches by 12 inches up to 96 inches by 140 inches,” Polkinghorne says. “Our equipment needs to keep that cutback the same across that area.” In addition to accurate measurement, this level of precision requires reliable motion control. In fact, it takes 28 axes of motion to properly control the conveyors and the X- and Y-axis movements of the film application head.
PDS IG needed flexible and open automation technology to ensure that the system and its various modules remained customizable. This way, they could easily integrate into customers’ existing systems and provide data for process optimization. As a result, they collaborated on the machine design with local sales and applications engineers from Beckhoff Automation. PDS IG first began using Beckhoff controls and components in 2011 at its Infinite Edge Technologies facility because it wanted to differentiate its controls platform from other companies in the market.
Don Seichter, area sales manager for Beckhoff, says this partnership has provided significant technological advantages: “Over the years, the ability to support numerous technologies in one control platform has helped PDS IG realize innovative applications that would have required multiple PLCs and black box technologies to come close to the same results.”
Automation solutions reflect flexibility and openness
The PDS IG window film application system relies on numerous Beckhoff technologies. For its operator interface, the system uses CP6202 “economy” built-in Panel PCs from Beckhoff. These panels, which combine a 15-inch touchscreen and a PC-based controller, are mounted to small electrical cabinets hung from the machine modules. “The CP6200 series allows us to run not only the HMI but also a thin client to increase modularity,” Polkinghorne says. “Depending on how many modules are used, a machine line that makes IG and applies protective film could span 100 feet. The thin clients allow users to navigate HMI screens for every machine module from any control panel.”
The machine control itself relies on a C6930 control cabinet Industrial PC (IPC) and TwinCAT 3 automation software from Beckhoff. TwinCAT 3 combines all functionality on a real-time control platform. TwinCAT 3 enables programming of the machines’ PLC, motion control, I/O and integrated safety in one environment. The CPU core-isolation capabilities of TwinCAT 3 allow PDS IG to designate these functions to run on a specific core of the C6930 IPC’s quad-core Intel® Core™ i7 processor. Before running the PLC, safety or other programs on the IPC in the field, engineers can design and test them using the object-oriented extensions of IEC 61131-3, computer science languages found in Microsoft Visual Studio®, a variety of built-in function blocks and other options in the graphical editor.

Polkinghorne says the TwinCAT Database Server also allows flexibility to collect production information in SQL databases on a controller or network connected to the Internet: “We have the flexibility to give customers the right data with the right frequency so that they turn it into actionable information to enhance production.” Further increasing efficiencies, TwinCAT can scan and automatically configure devices over ADS and the EtherCAT industrial Ethernet network, including third-party devices. This reduces point-to-point connections with USB cables during commissioning.
EtherCAT provides the fast, highly deterministic communication necessary for precise measurement and film application. In particular, the EL1252 digital input terminal with eXtreme Fast Control (XFC) technology from Beckhoff offers timestamping with a resolution of 1 ns. “Due to the complexity of the motion, we use XFC terminals with the TwinCAT 3 XFC library,” Polkinghorne explains.
EtherCAT also enables the use of TwinSAFE integrated safety technology to implement custom safety logic programmed via TwinCAT 3 and to communicate safety data over the standard EtherCAT network using a “black channel” approach. “TwinSAFE allows us to implement TÜV-recognized safety in a standard control platform and display safety-relevant information on the HMI,” Polkinghorne says. TwinSAFE programs load directly onto I/O modules with built-in logic, including the EL6900 TwinSAFE Logic Terminal, and other devices such as servo drives.
The window film application system uses a variety of Beckhoff motion control products for its 28 axes across the standard setup. The modules and film application head move with the help of powerful AM8000 series Servomotors. AX5000 series Servo Drives provide control and power to the servomotors via One Cable Technology (OCT). This has benefited multiple PDS IG applications, according to Polkinghorne: “One of our IG spacer application robots has 16 servomotors, so having just one cable for each is crucial for space savings in that solution — as well as the window film applicator.”
AX5000 drives also implement integrated safety through the addition of AX5805 TwinSAFE drive option cards. The cards offer drive-integrated safe stop, speed, position, acceleration and rotating direction functions. “Without hardwiring integrated safety logic, we can provide unique, flexible solutions to customers while still adhering to all safety requirements,” Polkinghorne adds.
Looking forward to future successes
The PDS IG Equipment window film application system achieved impressive repeatability, flexibility and cycle times before going to market in the second quarter of 2019. Using the high-speed measurement of EtherCAT XFC terminals, the applicator boasts a cutback precision of +/- 1/8 inch, even across the largest glass units it handles. “When applying this film on a 7- or 8-foot-long window, that consistency is pretty remarkable, especially considering how the film can stretch,” adds Rapp. Maintaining this high precision ensures IG units can be installed directly into the window sash without film becoming stuck when the time comes to peel it off.
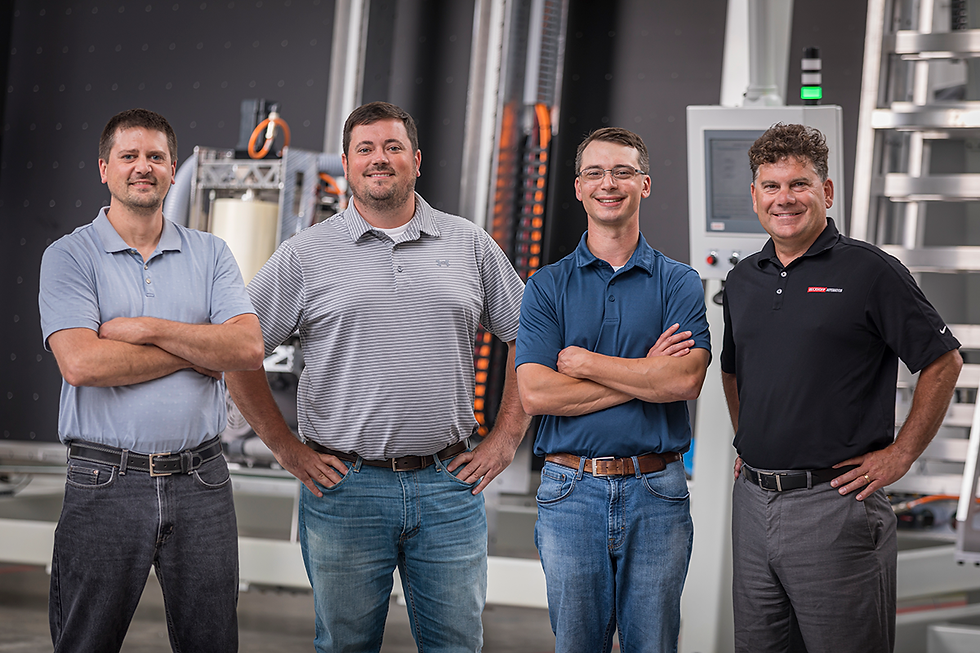
The flexibility and scalability of PC-based control from Beckhoff also reduced hardware requirements and offered valuable data to PDS IG and its customers. Accomplishing these results with another vendor would have required additional hardware PLCs and motion controllers.
Overall, the Beckhoff solution reduced costs while increasing openness, Seichter explains: “Beckhoff offered all the features PDS IG required in just one controller without the need for a specialized, single-purpose black box.” With flexible IPCs and TwinCAT 3, PDS IG provides customers with insightful machine health and performance data to help them maintain the system’s high throughput.
While glass dimensions vary from piece to piece, the PDS IG solution roughly doubles what is possible through other systems on the market, according to Rapp. “Our cycle times average 25 to 30 seconds per window, so the throughput for an eight-hour shift is about 1,000 to 1,200 IG units, compared to others in the industry that produce 500 to 600 in that same timeframe,” he says. “However, with flexible and scalable technology, our expandable system could add further modules to increase per-shift throughput to 2,000 IG units — even if each one has a different SKU.” With the ability to create increasingly comprehensive and efficient window production and finishing lines, PDS IG sees a future of continued innovation to better build and protect IG units in every circumstance, from the factory to home installation.
Ready to optimize your machine designs with a scalable, fully integrated automation platform? Contact your local Beckhoff sales engineer today.

James Figy is the Senior Content Specialist for Beckhoff Automation LLC.
A version of this article previously appeared in Control Engineering.
Comments