The Linear Progression of the XTS Adaptive Automation System
- Jeff Johnson
- Jan 22
- 5 min read
Beckhoff’s proven XTS technology continues to empower flexible, scalable, and hygienic manufacturing solutions

Not every journey is linear. But the development of the eXtended Transport System (XTS) has taken a constant, unwavering path. This has allowed engineers across industries to redefine what’s possible in material handling, assembly, packaging, and other applications – down to Lot Size 1.
In my recent webinar, we explored where the idea for this intelligent electromagnetic track system came from and how it has evolved over the years to meet new customer needs. It was exciting to share how this groundbreaking solution continues to redefine motion control in modern manufacturing.
We greatly appreciated the insights from Tom Brooker, Vice President of Engineering at Bartelt Packaging, a ProMach Product Brand. Tom shared Bartelt’s story about how they harnessed adaptive automation using XTS.
The webinar recap below covers many of the key points of presentation, while answering some of the top questions we received. If you missed the webinar or would like to watch it again, please fill out the form to access the full on-demand video:
The linear progression of XTS technology
The story of XTS began in 2008 when Beckhoff collaborated with Bosch Packaging (now Syntegon) to develop the core concept. At that stage, it was more of an ambitious idea than a market-ready solution. However, this initial effort laid the groundwork for what was to come. The product’s global launch took place way back in 2012.
Since then, we’ve continued to innovate with additions such as higher-payload rail system from HepcoMotion, curved motor modules, Track Management, powered end effectors with No Cable Technology (NCT), and the IP69K XTS Hygienic for washdown applications. It’s incredible to see how far we’ve come. What started as a rough idea has grown into a robust adaptive automation platform that’s transforming the manufacturing landscape.
What made – and still makes – XTS revolutionary
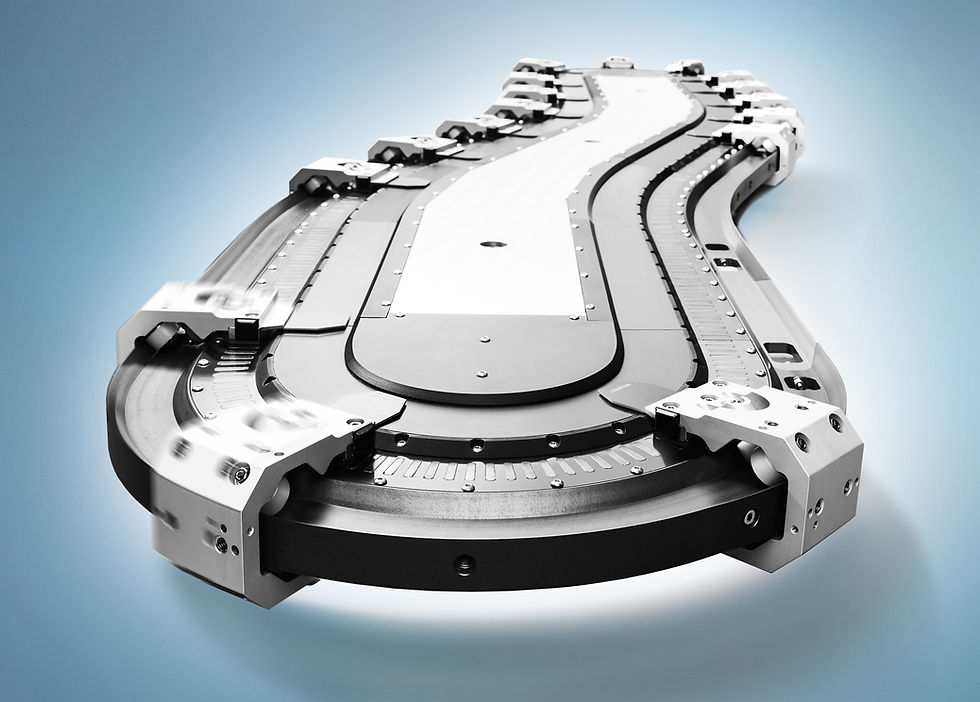
The core innovation of XTS lies in its ability to enable decoupled motion and an essentially infinite pitch. This flexibility allows manufacturers to efficiently adapt production processes, complete instant software-based changeovers, and shrink machine footprints.
The infinite pitch design lets customers configure their setups precisely to match their production needs. This ability to dynamically adjust processes is a game-changer for manufacturers. By eliminating the need for mechanical changeovers and relying solely on software adjustments, XTS delivers unprecedented flexibility and efficiency.
Bartelt makes the linear progression circular
One of the highlights of the webinar was discussing our collaboration with one of our machine builder customers, Bartelt Packaging. Based in Sarasota, Florida, these innovative engineers leveraged XTS to develop their innovative magnetic rotary pouching machine: the MAG-R.
Bartelt’s solutions must meet the high standards of food packaging applications. So they put our XTS Hygienic and standard tracks through their paces in rigorous testing, wanting to validate the capabilities we promise on their own.
Using a fully circular XTS track made of 22.5-degree motor modules, the MAG-R system debuted at PACK EXPO International 2024. And this video from the show floor shows just how stunning the results were.
Accelerating development for the path ahead
As with our efforts with Bartelt, customer cooperation and real-world feedback remains at the heart of XTS development. Through these collaborative efforts, we’re able to continually refine and improve our offerings.
It was rewarding to share the story of XTS — its origins, its innovations, and its impact — during this webinar. And I look forward to seeing how XTS continues to empower manufacturers and shape what’s next in automation.
Follow up from our XTS adaptive automation Q&A
We received some great questions during the webinar. Here are a few that we wanted to address in writing for anyone to see.
Q: One video showed movers being transferred from one track to another. Can this be done in different, more complex configurations to route movers to other tracks and control traffic?
A: Yes, this is possible. Track Management is a very flexible capability of the XTS system that can be applied to any number of different track topologies. You can watch how KOCH Packaging applied Track Management to a more complex system in this video.
Q: Also, can the movers be de-energized independently so they can be clamped at a station which may move the mover slightly to clamp it in place? The idea is that if they are de-energized, then they won't fight the clamp.
A: Absolutely. They can be fully de-energized and disabled independently. Alternatively, you could put movers into a "force-control" mode, which allows them to fight the clamp with a software-configurable amount of force.
Q: Do the XTS NCT movers lose power on the curved portions. Also, is 24 V DC the only output voltage option to I/O or other devices on the movers?
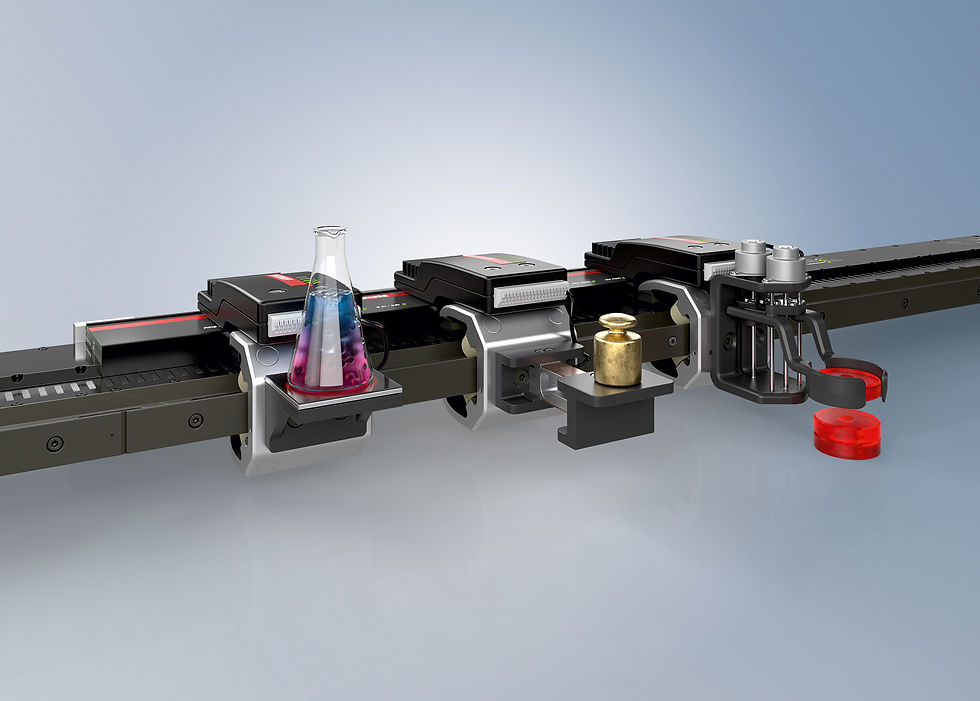
A: Correct on both counts. NCT-equipped movers will lose power on the curves. Currently, the only NCT motor modules are straight units. Without power, the end effector will remain in the same position it was in previously, so product will not be dropped. This also means you can space out NCT motors to the process stations and use standard motor modules in places where the end effectors don’t need to perform tasks, reducing system costs.
Regarding the second part, the NCT movers offer 24 V DC digital and analog I/Os as well as PWM. The PWM outputs could be used to generate a lower voltage, if necessary, but that would require some testing to ensure we could drive the device. The full pinout is available on our website.
Q: Are there any special considerations for mounting the track vertically vs. horizontally?
A: The system is fully capable of operating in any orientation, but there may be application considerations. System sizing is one such consideration. Lifting a very heavy load against gravity will impact power requirements and the overall thermal load. In some cases, we may be able to move the load around the curve of a vertically oriented track but not able to stop and hold in the curve if the system is at its peak current range.
You also need to consider system behavior when an E-stop is engaged while the movers are on a vertical curve. Without motive power applied, movers will fall out of the curve which could create a crash scenario.
Q: For performing a press operation, does it matter which orientation the force of the press is acting?
A: We work closely with Hepco to quantify the effects of all effective loads on the rail system and to validate feasibility. Hepco performs a thorough mechanical analysis based on the tooling, product loads, and press forces. In general, external forces should be directed through the bearings with minimal cantilever where possible. A best orientation may depend on application-specific factors.
Q: Does XTS offer integrated safety? Can safety zones be established that can be controlled independently?
A: No, the XTS itself doesn’t have integrated safety – at least, not currently. Today, motive power is brought to the track segments in zones, so sections of the track can be disabled independently. Control power remains in these situations, for example, so that mover position isn’t lost even during an emergency stop.
Integrated functional safety, which is well known from our drive technology portfolio and other products, is on the roadmap for XTS and in development. So, stay tuned.
Ready to redefine what’s possible using proven XTS adaptive automation tech? Contact your local Beckhoff sales engineer today.
Check out our upcoming and on-demand webinars to stay current on automation innovations.

Jeff Johnson is the Mechatronics Product Manager at Beckhoff Automation LLC
Comments